Projects
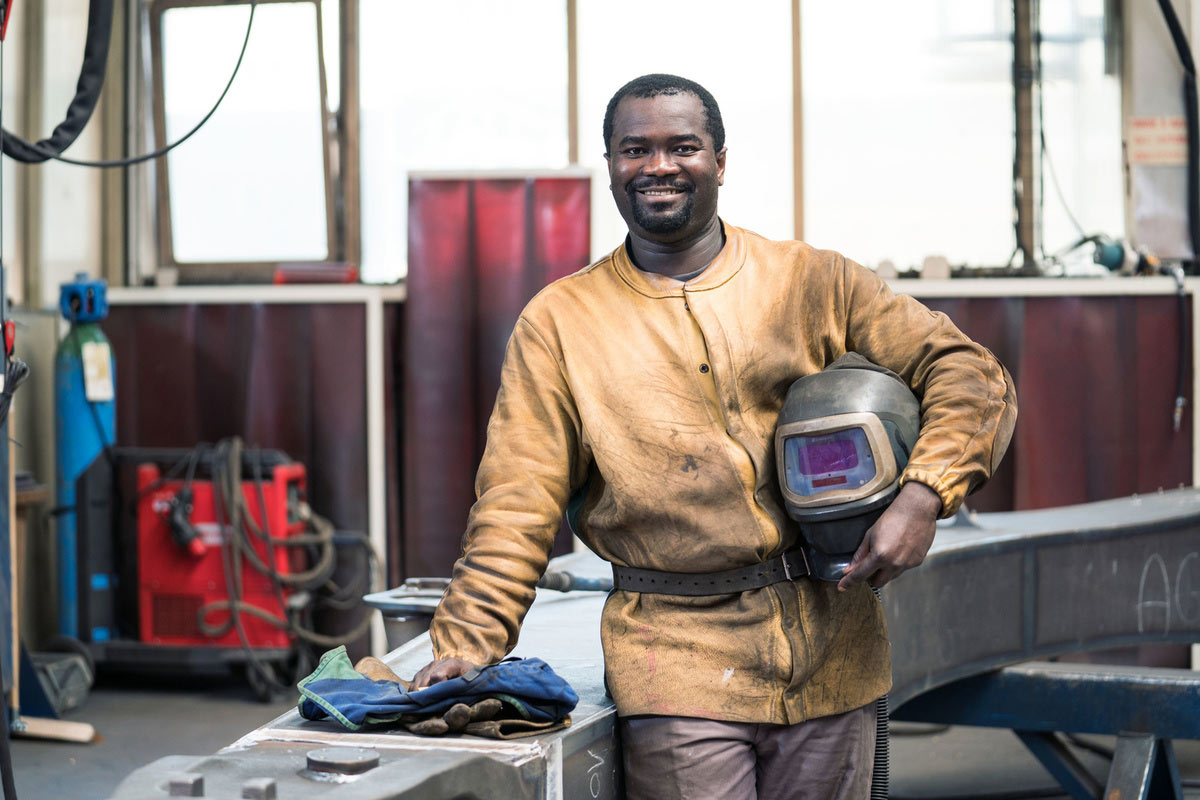
Workplace ergonomics
Everyday working conditions should be adapted to the activities being performed and the needs of our employees. Our goal is to create the absolute optimum working conditions. The most important features we provide on our premises include
– ample daylight in working areas,
– preventing reflections and glare on work surfaces,
– enough space for office furniture, machinery and equipment,
– sufficiently wide circulation routes and height-adjustable desks to create additional opportunities for movement, by alternating between sitting and standing activities.
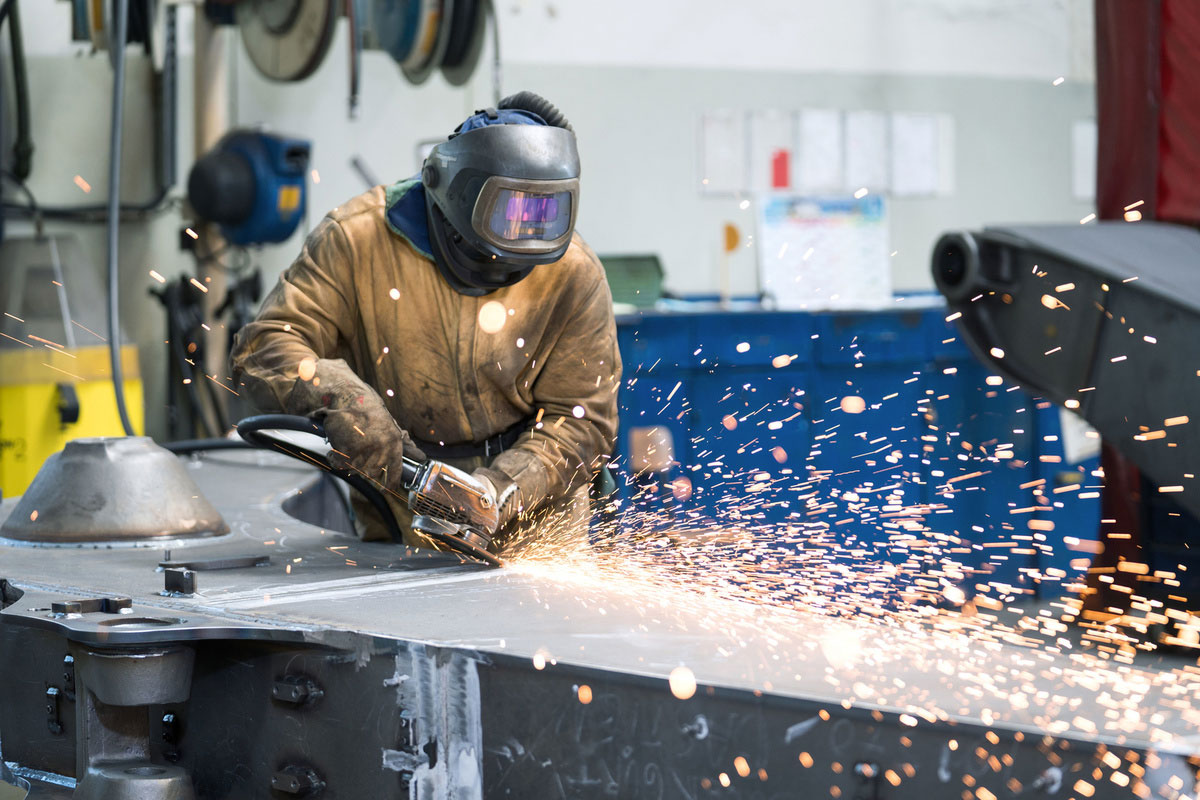
State-of-the-art technology – Welding Robots
Welding is one of Liebherr’s core competencies. The complexity of demanded welding seams is high and therefore our welders are highly qualified specialists in their field. Due to this fact, robots will never substitute the sophisticated skills of our welders, but: a welding robot can perfectly support them in their daily work by performing less complex tasks in an unbeatable speed. Because of their welding expertise, our team leaders are doing their bit in the acquisition process of such a robot and therefore are dealing with additional tasks:Defining requirements for the installation of the robot including clamping devices, choosing the right workers for on-the-job training on the welding robot, defining safety measures, optimizing working processes on a regular basis and conducting acceptances at the supplier’s premises.
In order to guarantee the perfect functionality of a multiaxial welding robot we have to attach great importance to the programming of the machine. Precise programming helps to minimize errors and is avoiding bigger interventions into the program through our welders therefore increasing efficiency. It is planned that our apprentice workshop will soon have a welding robot at their disposal, ensuring that prospective welding specialists are familiar with state-of-the-art technologies.
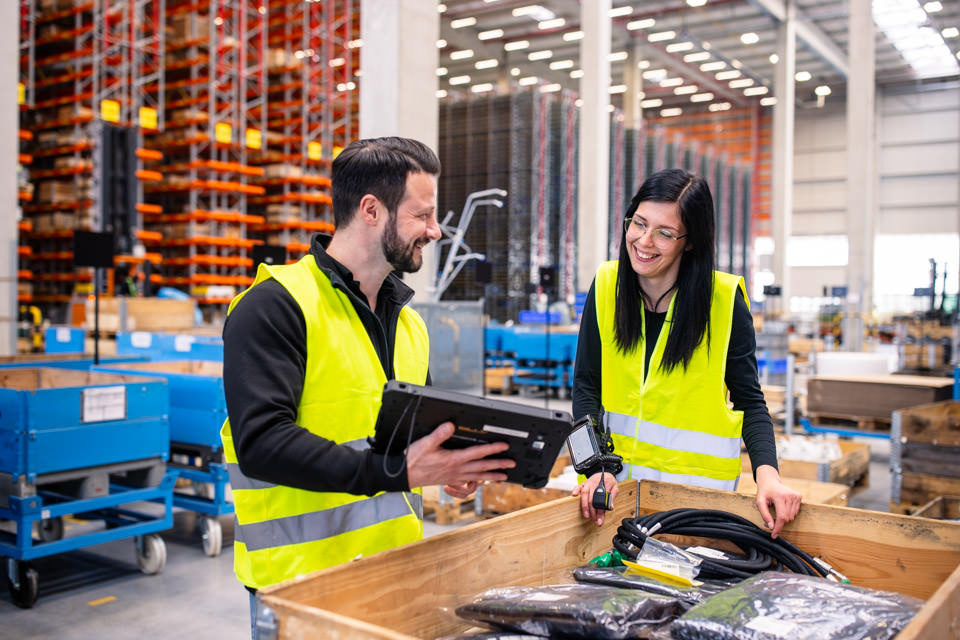
Supermarket principle in logistics
Supermarket pull systems are used in lean management to link work stations that are not in a continuous flow. At the Liebherr plant in Telfs, Austria, these systems are used to link the main warehouse and selected assembly stations. In the logistics supermarket, heavy and small parts are prepared into assembly-ready sets. This enables continuous one-piece flow at the subsequent work stations. In addition, it reduces setup times and inventories on the assembly lines.
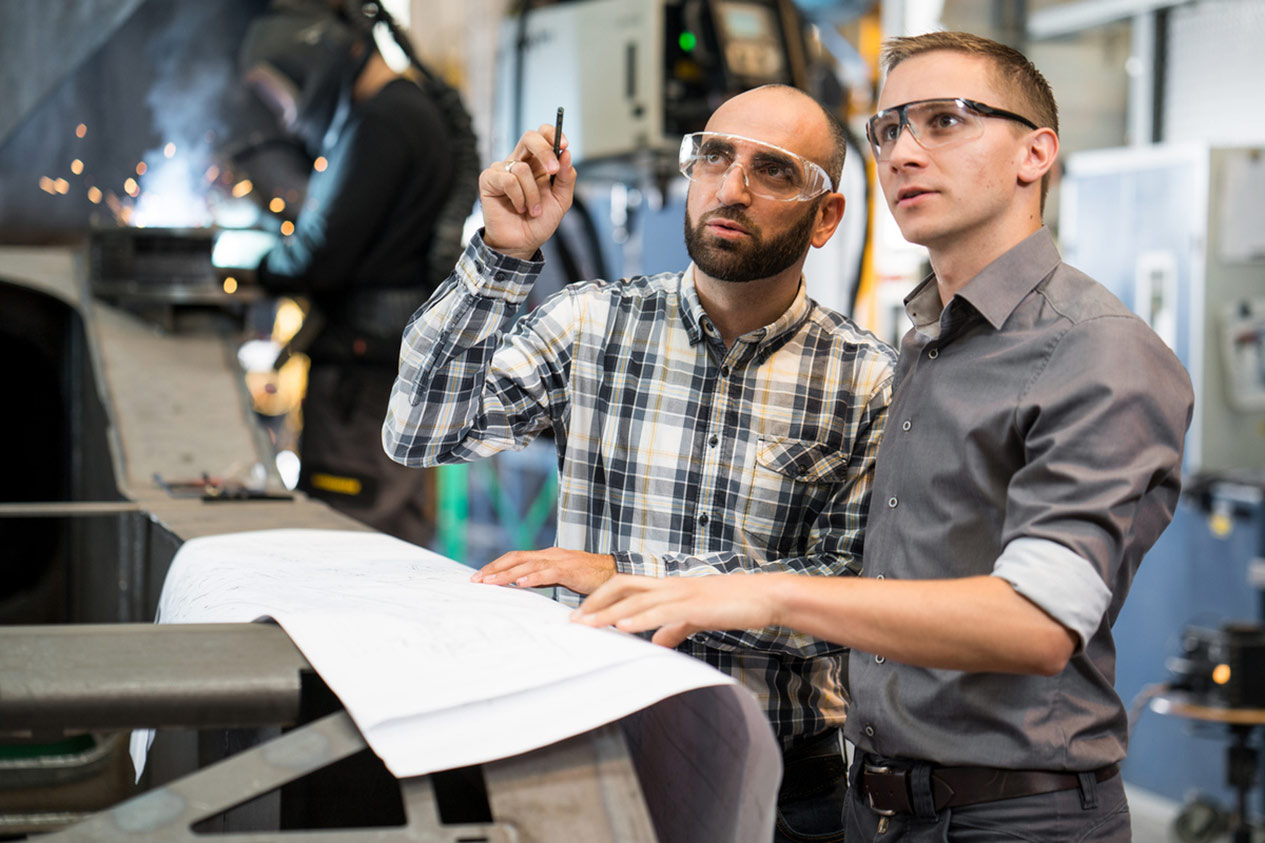
Optimizing the flow of communication – shop floor meetings at Liebherr
With the introduction of shop floor management in assembly at our Liebherr plant in Telfs, Austria, many meetings and decision-making paths have become shorter. The entire workforce – from production workers to the CEO – is involved in regular shop floor meetings at various levels, thus ensuring a continuous flow of information and decision-making. In addition, relevant metrics are visualized and tracked on each level. In this way, we all pull together and help achieve the company’s goals