Efficient exhaust gas aftertreatment
Liebherr meets the increasingly stricter emissions standards with systems expertise. We developed our own exhaust gas aftertreatment systems, which are optimally combined with our diesel engines. These systems reliably reduce exhaust gas emissions and harmful particles.
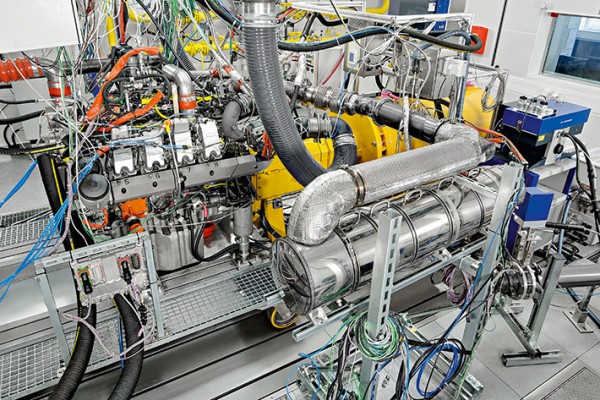
D9508 diesel engine: Nitrogen oxide and particle emissions are measured at the test bench.
Vertical integration has a long tradition at Liebherr. We manufacture key components and systems ourselves. In view of the stricter emissions standards, we decided on our own injection system including engine control. Liebherr offers a standard basic engine. This engine can be flexibly adapted in accordance with the modular principle with small modifications or by exhaust gas aftertreatment systems. In this way we are able to meet the different emission regulations of different countries and regions with one engine architecture.
Modular system for every emission standard
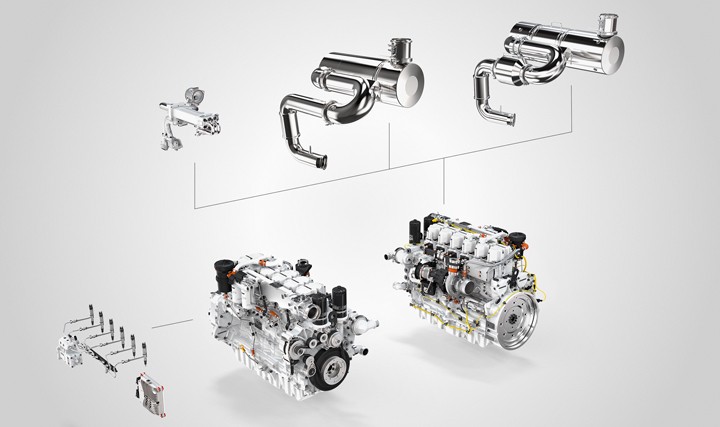
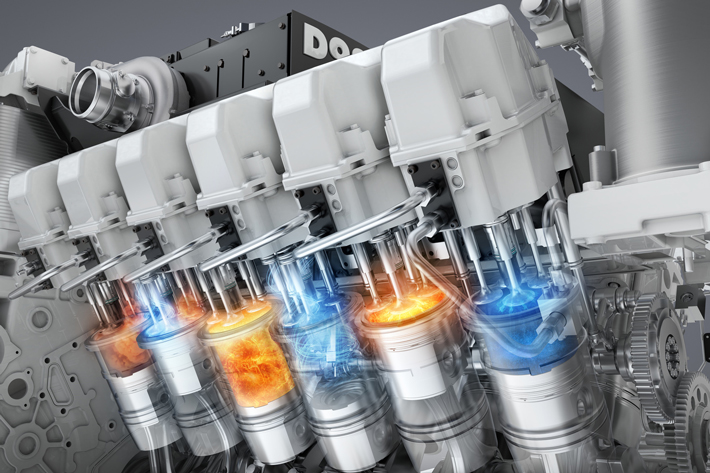
Fuel optimised engine configuration
The fuel optimised basic engines without exhaust gas aftertreatment are ideal for unregulated markets. They are extremely robust and work very reliably with fuels of different qualities.
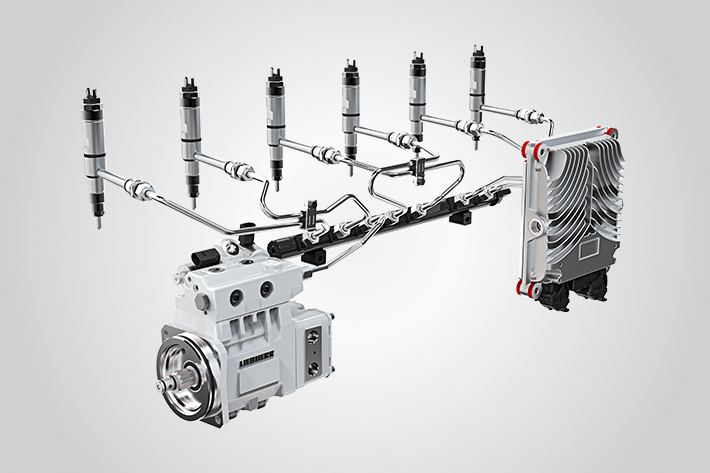
Common Rail system
The injection system from Liebherr is ideally matched to the engines - for high performance capability with low consumption.
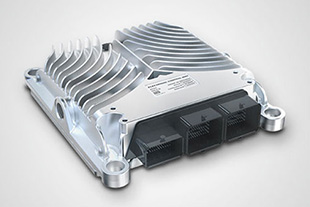
Engine control unit
In addition to injection and the combustion process, the electronic engine control also regulates the exhaust gas aftertreatment.
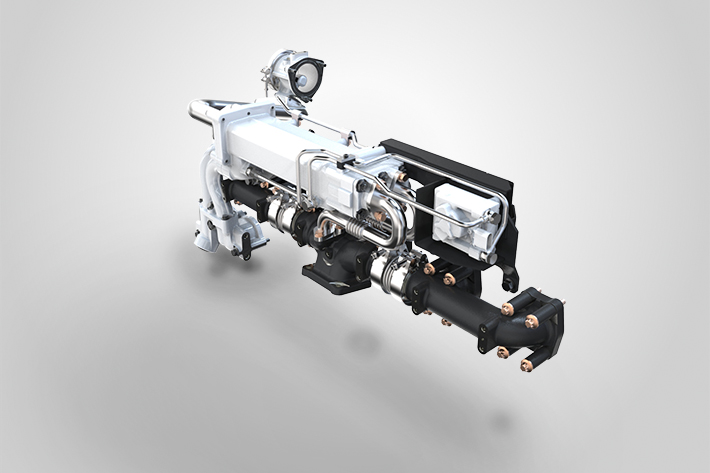
EGR technology for Stage IIIA compliant
The basic engine is equipped with exhaust gas recirculation for slightly regulated markets. This recirculation reduces the nitrogen oxides and guarantees compliance with limit values. The recirculation of part of the exhaust gases entails a lower concentration of oxygen within the engine air. The combustion temperature as well as the nitrogen oxides produced can therefore be reduced.
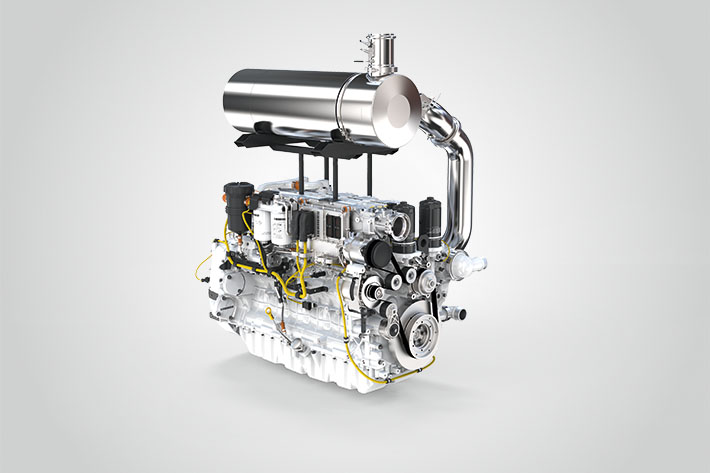
SCRonly for Stage IV and Tier 4 final
In order to comply with the emission limit values of Stage IV and Tier 4 final, Liebherr diesel engines only require the SCRonly system - no further technologies, such as particulate filters, exhaust gas recirculation, or DOC catalytic converters, are needed.
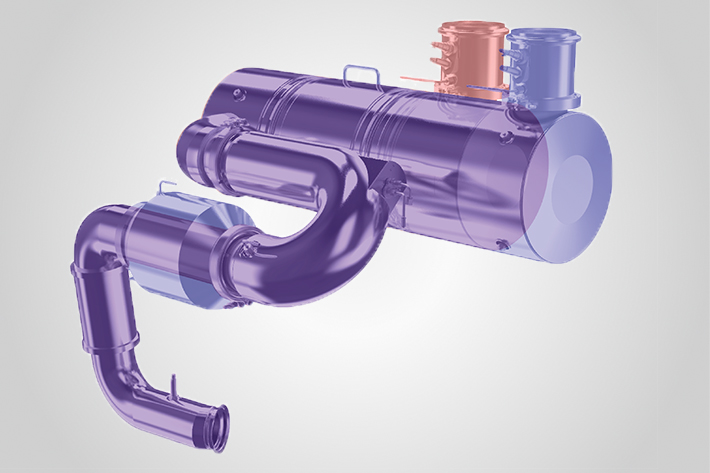
SCRFilter for Stage V
The SCRFilter system designed by Liebherr incorporates a DOC catalytic converter, an SCR catalytic converter, and an SCR-coated particulate filter. Compared to its preceding EATS solution for stage IV (SCRonly), SCRFilter has only gained 20% in length and offers a very compact solution in accordance with emission standards EU Stage V (effective from 2019). Within heavily regulated markets like Switzerland or the tunnel boring industry, the system has been already in use since more than one decade.
Strategy for emissions stage V
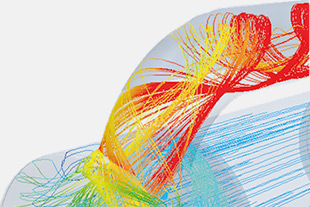
Flow analysis of SCR system
Liebherr is already preparing for stage V of the European emissions limit values from 2019 and has developed the innovative SCRFilter system. This system is already used in machines for tunnelling and is certified for stage IV, as well as the Swiss market. The Liebherr solution comprises a DOC catalytic converter, a SCR catalytic converter and a SCR-coated particulate filter. The maintenance-friendly technology permits easy access to the new SCRFilter. The filter needs to be cleaned after 4,500 working hours at the earliest and this can be done in Liebherr's own Reman centres.