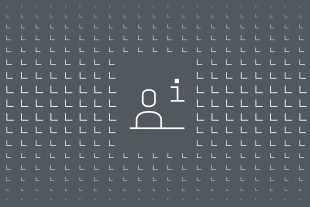
Joachim Dobler
Liebherr-Werk Nenzing GmbH
Dr. Hans Liebherr Straße 1
6710 Nenzing
Austria
- Phone+43 50809 415-74
Just a few months after the launch of SmartGrip®, ports across the globe rely on this innovative tool and its outstanding advantages, including Necotrans in Senegal and Port Polnocny in Poland. Operating as an intelligent system, SmartGrip® optimises grab filling rates in a self-learning manner.
After the launch of SmartGrip® in June 2014, many customers approached Liebherr and expressed their interest in this innovative technology. In the meantime, several cranes all over the world have already been equipped with SmartGrip®, which stands for more turnover, less stress and zero overloads. This technology for optimised grab filling rates is not only available for new cranes but also suitable for retrofits of existing cranes.
Two LHM 550s with SmartGrip® to start operation for Necotrans
Founded in 1985, Necotrans has vast experience in freight forwarding and port management with branches all over the world. Recently, Necotrans decided to invest in their port infrastructure in Dakar, Senegal, where two LHM 550s will soon start operation.
The tasks of both machines include bulk operation and container handling. Due to the positive feedback SmartGrip® has already generated, Necotrans decided to install this innovative technology right from the start. Thus, the company ensures highly efficient handling of bulk material without overloads harming the crane structure.
Port Polnocny equips existing LPS 600s with SmartGrip®
In 2013, two LPS 600s started operation in Port Polnocny, Poland. Both machines are equipped with the unique Pactronic® hybrid power booster. This cutting-edge hydraulic hybrid drive for cranes allows for a plus of 30% regarding turnover capacity. At the same time, Pactronic® leads to a reduction of fuel/energy consumption (litre/ton) as well as CO2 and exhaust emissions in the range of 30% depending on the operation.
Like others, Port Polnocny is constantly looking for new ways to enhance productivity. The acquisition of both LPS 600s equipped with Pactronic® was an important milestone for the port. The launch of SmartGrip® offered a new possibility to increase efficiency. After the installation of this new technology, the first cycles have already demonstrated the capability of intelligent grabbing.
“In our efforts to increase productivity, the installation of SmartGrip® was a logical decision. Our crane drivers are delighted with the new system, which ensures that we do not waste turnover caused by bad or volatile grab filling rates. Moreover, overloads are eliminated which means to a longer crane life,” said Adam Luczak, Port Polnocny’s Bulk Terminal Manager.
Thanks to the combination of both state-of-the-art technologies, SmartGrip® and Pactronic®, Port Polnocny simultaneously benefits from two Liebherr innovations.
SmartGrip®: Outstanding Advantages
SmartGrip® is the solution for optimised grab filling rates and provides valuable advantages including the elimination of overloads, less stress for the driver and higher turnover.
Changing materials and varying density are main challenges for the crane operator in bulk operation. Furthermore, density also depends on depth of impression which means that even when working on the same hatch, handling situation may change. If the driver needs to fill the grab manually, he may overload the crane when pulling the lifting attachment out of sticky material. Frequent overloads lead to a notably shorter lifetime of the crane and are also time-consuming. SmartGrip® controls the filling of the grab to suit the load curve of the crane, which leads to perfect crane utilization without overloading.
Bulk material handling comprises a number of challenges. To maximise productivity, the grab has to be filled to the limit, which means the driver has to fine-tune grab filling by opening and closing the grab as well as hoisting and lowering. This is both stress for the operator and time-consuming. When SmartGrip® is activated, the operator can completely rely on the system for an accurate determination of the material density and optimal grabbing angle in a very short time. The automatic and optimised grab filling means less stress for the crane operator who can shift the focus on other important issues like safety.
Achieved turnover depends on many issues, including available infrastructure, driver skills and materials handled. SmartGrip® optimises various parameters, allows for improved performance and significantly reduces turnover variance, leading to more efficiency in operation. Field studies showed that even up to 40% turnover increase are realistic if the grab filling rate is below average. Additionally, SmartGrip® partly closes the gap between high-skilled and less-skilled drivers, as some important parts of bulk handling are automatically optimised by the system.
Future installations in the pipeline
Due to the strong interest from its customers, Liebherr expects several new SmartGrip® installations in new and existing mobile harbour cranes in the near future.
Here you will find the press release and images for download.
Liebherr-Werk Nenzing GmbH
Dr. Hans Liebherr Straße 1
6710 Nenzing
Austria