You are here
Liebherr Group: Products & Services for Other countriesThe requirements for the production of combustion engines are generally known and exactly defined. However, the production of e-mobility components is still new territory for many users. Systems for battery pack assembly are mostly not yet designed to deal with large batch sizes and are therefore only partially automated, because complete automation is not yet economically viable for smaller and medium batch sizes.
When batch sizes increase, however, partially automated production is no longer efficient or economical. In order to be able to keep pace in growing markets, fully automated assembly lines are increasingly in demand by vehicle manufacturers and suppliers.
We have always considered ourselves to be solution providers and a point of contact for all customer concerns.
Automation provider with system capability
Liebherr has integrated this technological transition into the further development of its automation solutions and built up corresponding expertise in order to support its customers in the design of new manufacturing processes. The company designs manufacturing lines for both conventional and electrified drive systems and, with its modular automation solutions, covers all requirement profiles from individual stations to turnkey systems – whether it is for combustion engines or for e-mobility.
“We have always considered ourselves to be solution providers and a point of contact for all customer concerns”, explains Viktor Bayrhof, Market Sales & Product Management for Automation Systems at Liebherr, describing the company’s aims. “Because of the changed requirements made of automation in e-mobility, we are currently changing from being an automation specialist with a focus on material flow technology to a system supplier with process competence.”
Core processes in battery assembly: dosing and screwing
With regard to these requirements, various subprocesses in battery pack assembly play a decisive role. These are mainly dosing and screwing processes:
- The dosing and application of the heat-conducting and electrically insulating gap filler, a heat-conducting paste for the thermal connection and cooling of the electrical components
- Inserting and screwing the modules into the battery pack
- Applying and screwing on the battery lid, and applying the sealant so that no gases can escape or moisture enter the battery
Other important modules are critical and safety-relevant processes at the end of the manufacturing line, such as the leak test and the end-of-line test (high-voltage electricity test), as well as the integration of the associated test benches into the manufacturing line. Here, solutions are being developed for how to transfer a battery pack from the manufacturing line to the test bench. But extreme scenarios, such as the case of fire, are also being considered and emergency strategies developed.
Automated plugging of module connectors
Liebherr pays special attention to the electrical contacting of high-voltage module connectors (busbars). These can be plugged, screwed or welded. Pluggable module connectors present significant advantages compared with screw connections. For this, Liebherr has developed an innovative and unique automation process with which this type of plug connection can also be plugged with process reliability (more information here).
From subprocesses to a complete system
The components for the individual processes are supplied by specialist suppliers; for dosing processes, for example, the dosing equipment, including the pump, metering unit and process monitoring system, are bought. Liebherr integrates these into its own robot cells and supplies a turnkey automation solution for the customer-specific process. This may mean integrating process stations into a complete system conceived by Liebherr; however, if required, Liebherr can also offer a single station.
“We consider the process from inside out – from the individual process in detail to the individual robot cell, right up to the complete system. We can test and validate all this on our own test systems under real conditions”, explains Jan Pollmann, development engineer for automation systems. “If we imagine the individual components of automation as being like a Lego building block, here in the Tech-Center we have already built a small Lego city and got it up and running.”
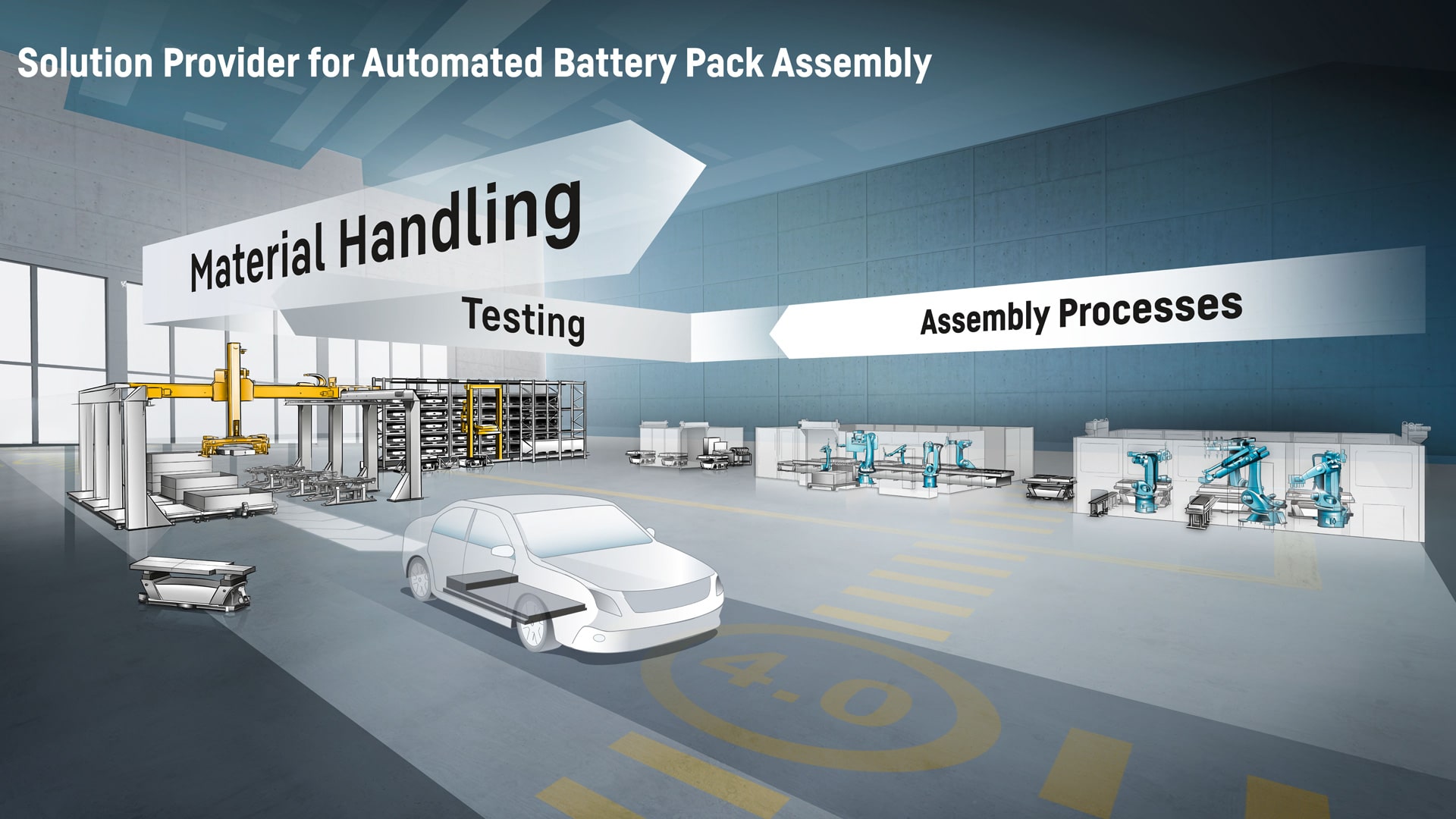
Unique possibilities in the Tech-Center
Over 700 m2 of testing space, Liebherr carries out feasibility studies and preliminary tests in its own Tech-Center. Subassembly lines with technology modules for the automatic production of battery packs (screwing, plugging, dosing, bonding, gripping, positioning) are available there for tests and quality control of components and processes.
Liebherr thus offers the possibility of testing and validating processes under real conditions. Tests can be presented to customers on site but also virtually using cameras. With test series commissioned by customers, Liebherr is flexible and quick to respond: “If the customer wishes to test a process directly on the workpiece, we can build a test line for this within a very short time”, explains Jan Pollmann. “These core processes can then be scaled up to the series system for volume production.” In order to fulfill as many customer requirements as possible, the individual process stations are equipped with different robot types from Kuka, Fanuc or ABB.
Competence center for e-mobility
This enables Liebherr to advise customers comprehensively on the design of new processes, thus preparing them for the forthcoming technology transition, whether it is for subprocesses or for the entire assembly line. The modular approach offers the greatest possible flexibility, whether it is in the integration of manual workstations or the subsequent retrofitting of automation processes due to rising batch sizes. “This means that the degree of automation can ‘grow with the company’ according to individual customer requirements. System capability means that we can combine all the process modules into a complete system”, says Viktor Bayrhof in summary.