You are here
Liebherr Group: Products & Services for Other countriesBright light floods through the large windows of the hall roof. The large rotary loading system from Liebherr can already be recognized from afar. It is installed upstream from a machining center, where up to 63 different components can be milled for various water pumps. Michael Wizany now clamps a new raw part at the set-up station of the RLS 800. It is then precisely moved to one of the 21 storage locations in the rotary loading system by means of a rotation shuttle or directly placed at the machine for machining.
In the mechanical pump manufacturing at Rosenbauer, water pumps are developed for various applications. In addition to fire pumps, which are installed in fire trucks, submersible pumps or stationary motor pumps that are used for the protection of industrial companies or in flood protection are also part of the product portfolio of the Leonding-based company. Pump parts, which are manufactured with help of Liebherr automation, are later used in vehicles of the AT line. AT stands for Aluminum Technology, as the frame, which is also developed by Rosenbauer and later combined with the chassis, is made from aluminum. The water tank of those vehicles can hold up to 4,000 liters of extinguishing water. They are used as conventional fire trucks for countless dams and account for around 55 percent of the annual turnover.
When choosing such a machine, we pay great attention to the manufacturing company. We obtained a fully developed concept with the solution from Liebherr
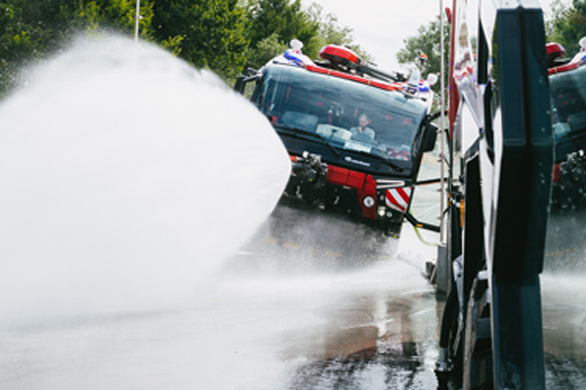
Enormous increase in productivity thanks to Liebherr system
One machining center follows the other in the production plant and there is not much storage space. The automation solution from Liebherr is designed precisely for restricted spaces. “We can store up to 21 pallets in the RLS in a confined space. The entire system also takes into account the individual delivery dates and can be adapted dynamically – depending on prioritization”, is how the machine operator Michael Wizany explains the benefits of the Liebherr system. If a new part is coded in the system, the automation solution automatically recognizes recurring components. “With the use of the rotary loading system we achieve time savings of up to 50 percent”, states the 28-year-old about the enormous increase in production efficiency. Thanks to the rotary loading system the machining center can also be supplied with parts without any manual intervention, which is beneficial particularly after the end of a shift. “We work in a two-shift operation, but can continue to produce up to four hours after the end of a shift thanks to this automation. The next morning, the employee unclamps the parts machined overnight and can perform new clamping processes”, explains Production Manager Michael Schöftner. Schöftner and his team appreciate the stable, robust, and yet high-precision functionality of the Liebherr automation, as well as the fault-free and very reliable operational readiness of the RLS right from the start. “When choosing such a machine, we pay great attention to the manufacturing company. We obtained a fully developed concept with the solution from Liebherr”, adds Schöftner.
However, at Rosenbauer the individual employee is always the decisive factor – despite automation. “Our employees are experts in the area of mechanical production. The machine and the RLS must be programmed and monitored. This is a very responsible job”, states the 39-year-old. And his employee Michael Wizany adds: “Automation needs professionals”. Many employees are also active firefighters and contribute their experience to day-to-day work. Lifeblood for firefighting can almost be felt here.
Tests under real conditions
Nonetheless, before a vehicle leaves the factory premises in Leonding, the pump has to pass several stations of production. After the pump parts have been deburred, the density of the pump is verified by a pressure test. A job which also requires lots of expertise and sensitivity. Pump housings must withstand an operating pressure of up to 18 bar. Nevertheless, they are deliberately tested at 24 bar – this ensures that the parts withstand the high pressure during use.
Now, the finished pump has to be anodized. A protective layer is formed from the oxidation of the surface made from aluminum, which makes the pump housing extremely robust. When the pump is completed it is combined with the frame in plant II, which is only a few kilometers away from the main factory. “The frame made from aluminum is the framework for the structure, which is later positioned on the truck chassis”, explains Michael Schöftner, who has been managing mechanical production for two years. This structure can be individually designed and equipped – depending on the customer’s requirements. “Most of our vehicles are unique, we only manufacture our AT line in series production”, adds Schöftner.
A highlight product from Rosenbauer is the Panther. The vehicle was designed especially for use at the airport and can transport up to 19,000 liters of water in the tank. The main components, such as structure, cab, or chassis, are produced directly on site and have been for many years. The company’s history dates back to 1866. At that time, Johann Rosenbauer founded the company as a trading company for firefighting supplies. The company has been manufacturing fire trucks since 1906. Today around 3400 employees work at 16 production sites worldwide for the listed family-owned company, which achieved a turnover of 871 million Euro in 2016.
Human beings are indispensable.

Tests under real conditions
In addition to tests under real conditions, the Panther is also put through its paces on the factory premises and deliberately pushed to its performance limit, because the vehicle must perform its duty even under extreme conditions in the event of an emergency. Around 750 vehicles leave the Leonding-based plant every year and are used all around the world. Whether it is in the USA, Saudi Arabia, or South America – the Upper Austrian company manufactures its vehicles for diverse requirement profiles and standards. In addition, firefighting equipment, such as helmets or gloves, are also sold, meaning Rosenbauer has positioned itself as a Full-Liner for firefighting on the market.
When the chassis is coupled to the structure, the vehicle is individually laminated and fitted with the desired technical equipment. After all of this is completed, the big moment arrives– leaving the hall and the handover to the customer. Rosenbauer created a special customer center for this purpose, where the vehicles are handed over and the firefighters receive training on their new vehicle. In an Emergency Driving Response Simulator (ERDS), emergency drives can be simulated realistically on public roads.
But how will fire service develop in the future? Since the start of 2017, specialists from Rosenbauer have already been addressing the fire service of the future in a think-tank. In vehicle construction trend is clearly heading towards even more ergonomics and safety. “The vehicle is more and more approaching people. This means various equipment and tools can be extended automatically, which, in turn, considerably facilitates work for the firefighters”, explains Michael Schöftner. And even though automation arrived a long time ago in fire service, people remain the decisive factor during operation as well as in the production of fire trucks, as Michael Wizany concludes. “Human beings are indispensable.”