Mr Graner, how long has Liebherr been involved with alternative drive concepts and which have been used in real-life applications?
Klaus Graner: Essentially, Liebherr has been heavily involved in developing alternative drive concepts since the company was founded. With the invention of the tower crane in 1949, the firm’s founder, Dr. E.h. Hans Liebherr came to the conclusion that it was better to produce certain parts of the drive technology in house, as he was unsatisfied with what was available on the market. Thus, Liebherr has been developing and building electric machines and control boxes for its tower cranes in Biberach since the 1950s. As such, we have gained experience, particularly in electrical drive concepts, throughout the course of our history. Just as it did in the past, this helps us develop new drive concepts like diesel-electric systems for mining trucks. Liebherr has been producing complete mining trucks with this drivetrain for approximately ten years.
What applications and machines are the drive concepts best suited for?
Klaus Graner: This is not just a question about technology but more of an economic calculation, which is why diesel engines and hydraulic systems dominate the construction machine category. They benefit from high power density and being low on weight and on costs. When a business looks at investing in a construction machine, there are two key performance criteria: how many tonnes the machine can shift per hour the costs per tonne. This allows it to calculate when the return on investment (ROI) will be reached and the machine starts making money.
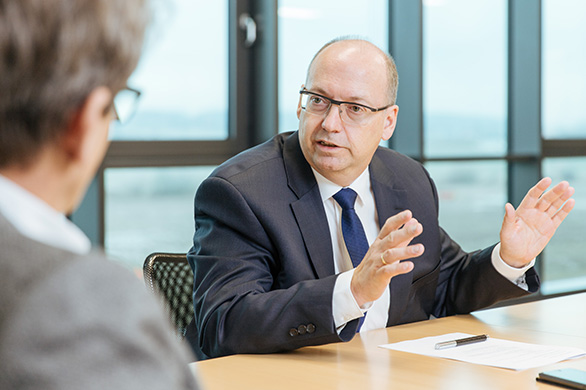
What does this mean for electronic drivetrains?
Klaus Graner: An electric drivetrain is more efficient than hydraulic solutions – with 90% and 70% efficiency respectively – and also achieves significant savings in energy consumption. However, it is much more expensive to procure. For example, compared with a diesel-hydraulic system, it takes many operating hours to recoup the additional costs of using a diesel-electrical system, due to the reduced fuel consumption. With construction machines, which operate up to 2,000 (but often only about 1,000) hours per year, this process obviously takes significantly longer than with machines such as mining vehicles, which operate for 5,000 hours or more.
When it comes to shifting heavy and super-heavy loads, the diesel engine has ruled the category since the beginning of mobility. What level does he think alternative drive systems are currently at?
Klaus Graner: First things first: Diesel is, and will continue to be, the standard for mobile construction machines for a long time. The fuel has an extremely high energy density, meaning that mobile machines can operate for up to 24 hours on a reasonably-sized tank of fuel. In addition, modern exhaust systems complying with increasingly strict EURO norms mean that emissions of pollution have continually fallen. Construction machine operators know exactly how important this can be. It remains to be seen whether hydrogen or synthetic fuels can replace diesel and take combustion technology to the next level in terms of CO2-neutrality. Because of their heavy weight, large volume and the high cost of batteries, I think purely electric transmissions are some way off being able to replace diesel completely.
What do you think about diesel-electric engines? Can they exploit the advantages in both technologies?
Klaus Graner: The benefits of diesel-electric transmissions are most obvious when it comes to high power applications and when dealing with very long operating times. Electrical power conversion has a 90% efficiency ratio – 20% higher than mechanical-hydraulic solutions. This affects energy consumption which in turn impacts CO2-emissions. Our analysis suggests that in the current circumstances it only makes economical sense to use diesel-electric engines starting at around 5,000 operating hours per year, as is the case predominantly in the mining category. In the case of smaller machines, it could be interesting in the future if, like in the car industry, there are legal targets and restrictions relating to CO2-emissions for individual machines, or for whole fleets or motor parks.
How real a possibility do you think that it is that legislators will create rules of this kind?
Klaus Graner: It would be naive to think that governments would only hold the car industry accountable for protecting the environment and forget all about construction machines. Nevertheless, nobody knows whether these types of regulations are coming, and if so, when. We are therefore continuously developing alternative drive technologies so that we will be well prepared when it does
How close are we to emissions-free construction sites?
Klaus Graner: Because fossil fuels still account for a large portion of overall energy consumption today, discussions about emission-free construction sites tend to be restricted to ‘local zero’ emissions. To achieve truly CO2-neutral construction sites on a global level, they would obviously need to be powered by renewable energy; in other words, it would take an energy revolution. We are developing suitable technologies and components for fully electrical construction machine drivetrains. However, it will be up to policy-makers, not developers or financially-driven machine operators, to decide whether we can at least achieve local zero emissions on construction sites in inner-urban areas. The additional costs entailed will only be paid when local zero emissions are enforced by law or regulations. Then, it will depend on the nature of the project whether to use batteries for energy storage on to physically ‘plug in’ machines. In the case of lengthier, more difficult applications, we would hit physical limits pretty quickly.
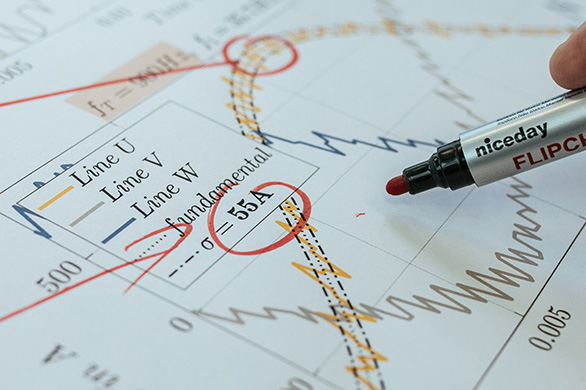
Can you give us an example?
Klaus Graner: Take, for example, a purely electric 50 kW wheel loader, designed to work continuously for 4 hours in the morning on an inner-urban construction site, and which is then recharged during the midday break so it can work for another 4 hours in the afternoon. The average power consumption at the drive shaft of an electric engine doing lighter work like this is about 12 kW. Over a four-hour period, this is equal to 50 kWh of energy. A battery with this effective energy content would weigh about 500 kilos, have a volume of 250 litres and cost around 30,000 euros. For jobs that are significantly more intensive and time-consuming than the one I have just described (for example, on large-scale earthmoving construction sites or in the mining industry), it seems more realistic and efficient to use combustion engines powered by hydrogen or synthetic fuels, both of which would ideally be produced in a climate neutral way in the future.
What kind of battery innovation do you think has the greatest potential?
Klaus Graner: The experts assume that the prevailing lithium-ion technology will continue to dominate the next 15 years. During that time, energy density may improve somewhat but it is pretty unlikely that there will be a quantum leap forwards.
Time is of the essence when it comes to climate change and the consequences for the environment, the economy and society. Are there any quick solutions? How long do you estimate it will take to develop alternative engines from the inception of the idea to being mass production ready?
Klaus Graner: Technologically, we have already made a lot of progress on the electric drivetrain. Now it's a matter of making it more compact with higher-rpm electrical machines, so that these drivetrains can be fitted on construction machines with sufficient ease. We estimate that it will take from three to five years to reach batch production. However, solutions involving battery-powered or plug-in construction machines will only help prevent climate change if the power is generated from renewable sources.
We are in close communication with customers inside and outside the company group throughout the development process. They know their work sectors and available budgets better than anyone else.
How do you do that?
Klaus Graner: We are in close communication with customers inside and outside the company group throughout the development process. They know their work sectors and available budgets better than anyone else. When we execute ideas, we combine the experience and expectations of our customers with the know-how and testing and checking infrastructure of the Liebherr-Components division. When creating innovations, it is helpful that we can sometimes adopt solutions from other projects and adapt them to fit our needs. This saves on time and costs.
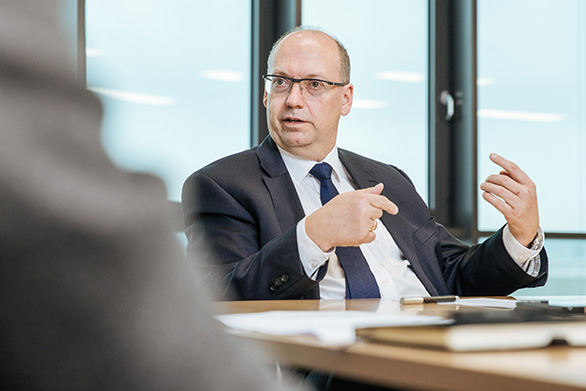
How are the efficiency and performance of alternative engines affected by being in challenging environments such as quarries and mines?
Klaus Graner: For some years, we have gained important experience from the fact that our diesel-electric engines are used in mining vehicles. As a result, it has become clear that we can achieve greater efficiency on upward slopes with more electrification. In some mines, these ramps stretch over more than five kilometres and span a height differential of up to 300 (500) metres at a ten percent incline. For current diesel-electrical mining vehicles, this means driving for around 25 minutes at full power. This accounts for about 90% of total fuel consumption. Since we have already had cases where machines operate for very long periods over exactly the same routes, we are already working with customers (for example, in Austria and Panama) to electrify the routes completely by using overhead lines and current collectors on our diesel-electric mining trucks.
Although this is possible in a mining setting, it would be far more difficult on temporary construction sites where the machines are constantly working in different areas. How mobile do you think electrification will be?
Klaus Graner: It is conceivable that there will be construction machines that drive to their work location using combustible fuel and then do their work there without requiring the mobility of a wheel loader, for example. This would enable them to be supplied with energy using a power outlet. One example of this would be a crawler excavator digging a hole with only a small deployment radius. This already happens with tunnel excavators, to prevent tunnel tubes from being filled with exhaust fumes. It would also be conceivable to use a cable connection to the power grid on a construction site, for example, for mobile cranes, concrete pumps or concrete mixers. As I mentioned before, for lower power requirements, electrical machines with a suitable battery would be just as mobile as conventional machines on construction sites.
Let’s think ahead: What drive concepts will be important in the future, and what are you doing today in order to make them a reality?
Klaus Graner: There is a lot of potential in an electronic drivetrain for a stepless power transmission. For intensive mobile heavy-duty applications, the same goes for using diesel engines built to the latest EURO norms as the vehicle’s the primary energy source, and, further into the future, for combustion engines powered by hydrogen or synthetic fuels. If we are able to successfully derive these alternative fuels from renewable energies so they are produced in a CO2-neutral way, it will be a big step forwards in terms of sustainability.
When will that happen?
Klaus Graner: It is difficult to predict, but it will definitely take more than 20 years before we reach the final step. But I am convinced that humanity will, and indeed must succeed in this regard. That much we owe to the generations to come. In any case, Liebherr is ready to contribute to a better future with its technologies and innovations. Of that, I am totally sure.