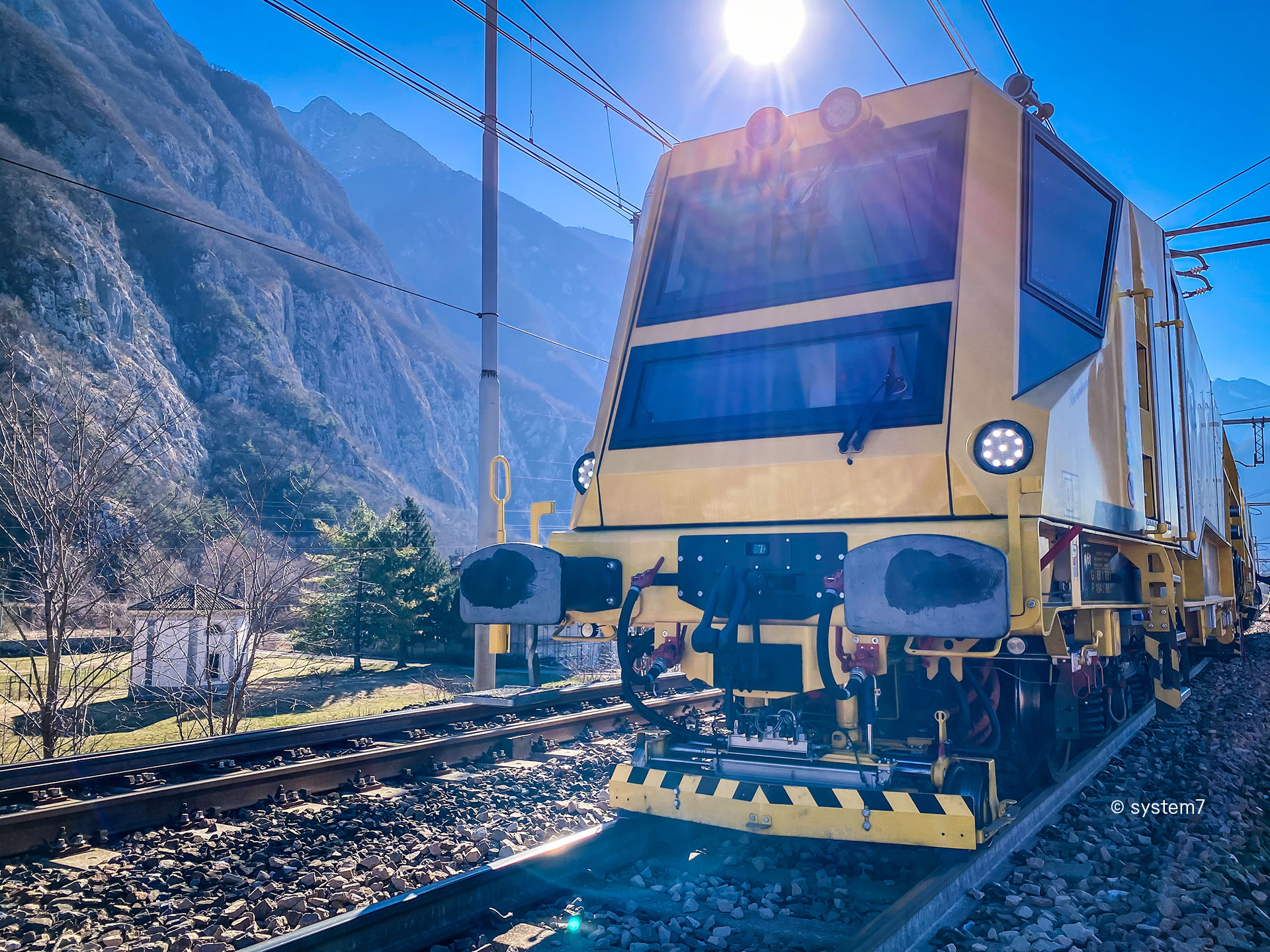
Jump on the bandwagon for 2023
Be it construction machinery, mining or aerospace, Liebherr components feel right at home, everywhere. However, we are willing to bet that you did not know that our electronics are also on rails. Find out more on how our digital cameras make the tamping machines of our customer system7 more safe and efficient.
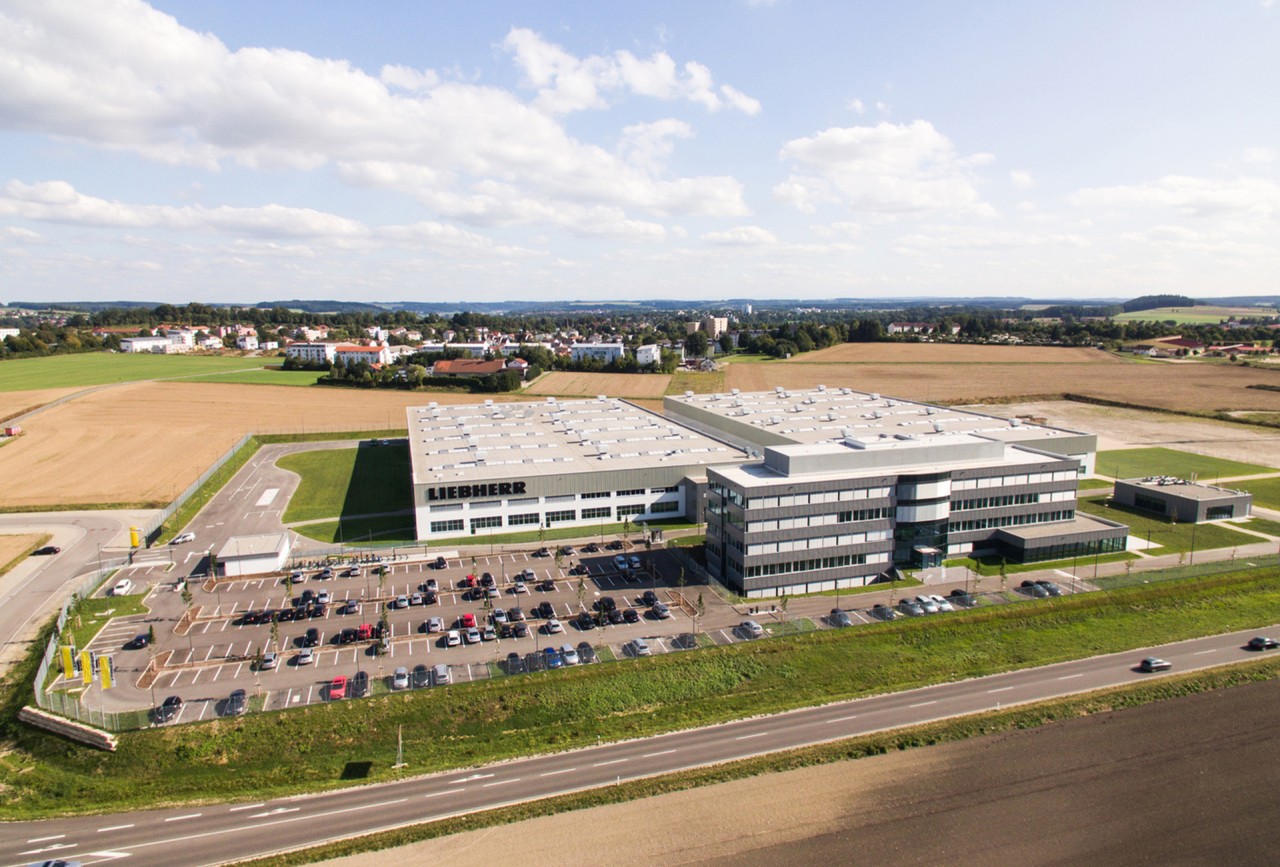
New year, new chapter
The start of 2023 has also brought a breath of fresh air to our German sites in Lindau and Biberach. On the first of January, Liebherr-Electronics and Drives GmbH came into being as a result of a merger of the two locations of the Liebherr Group's components product segment. This is a milestone that bundles our core competences into a uniform portfolio to master future challenges.
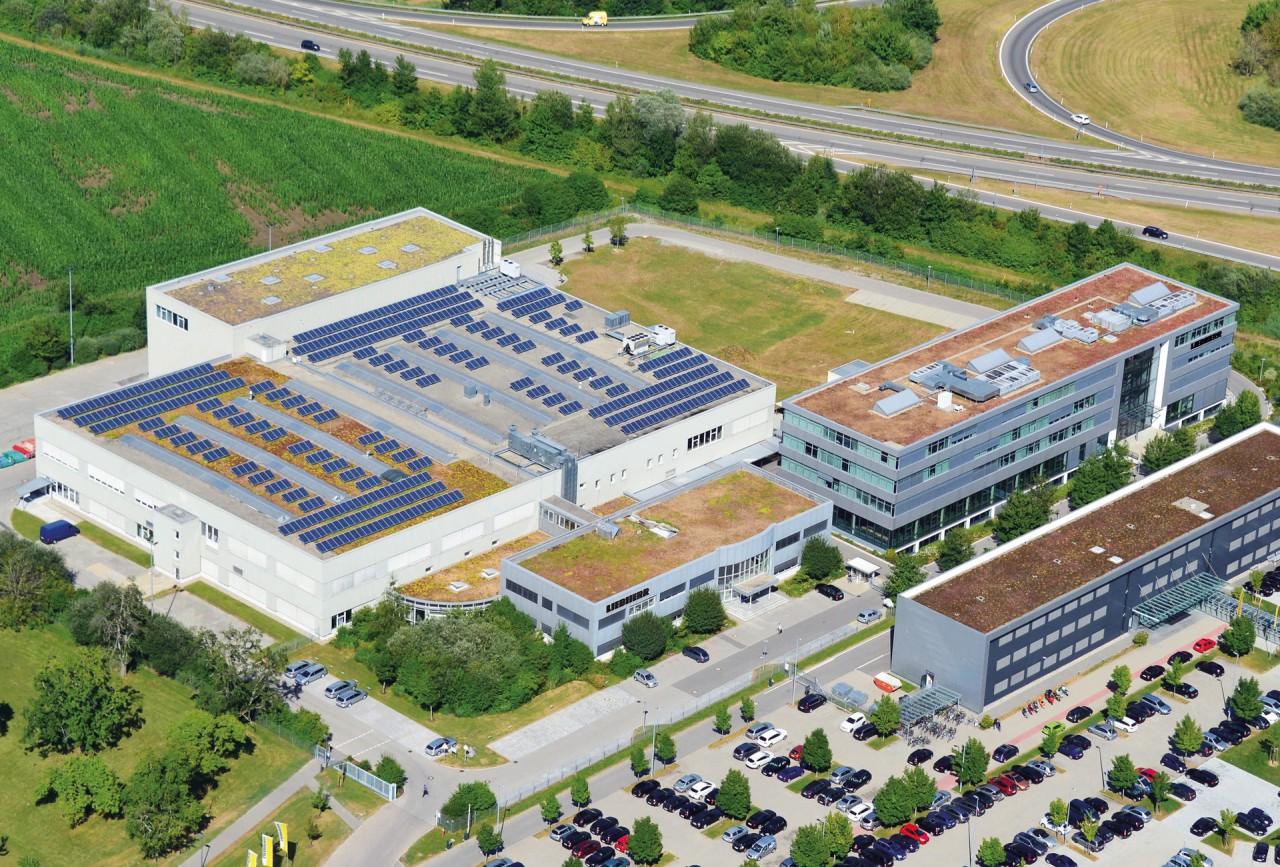
New year, new chapter
The start of 2023 has also brought a breath of fresh air to our German sites in Lindau and Biberach. On the first of January, Liebherr-Electronics and Drives GmbH came into being as a result of a merger of the two locations of the Liebherr Group's components product segment. This is a milestone that bundles our core competences into a uniform portfolio to master future challenges.
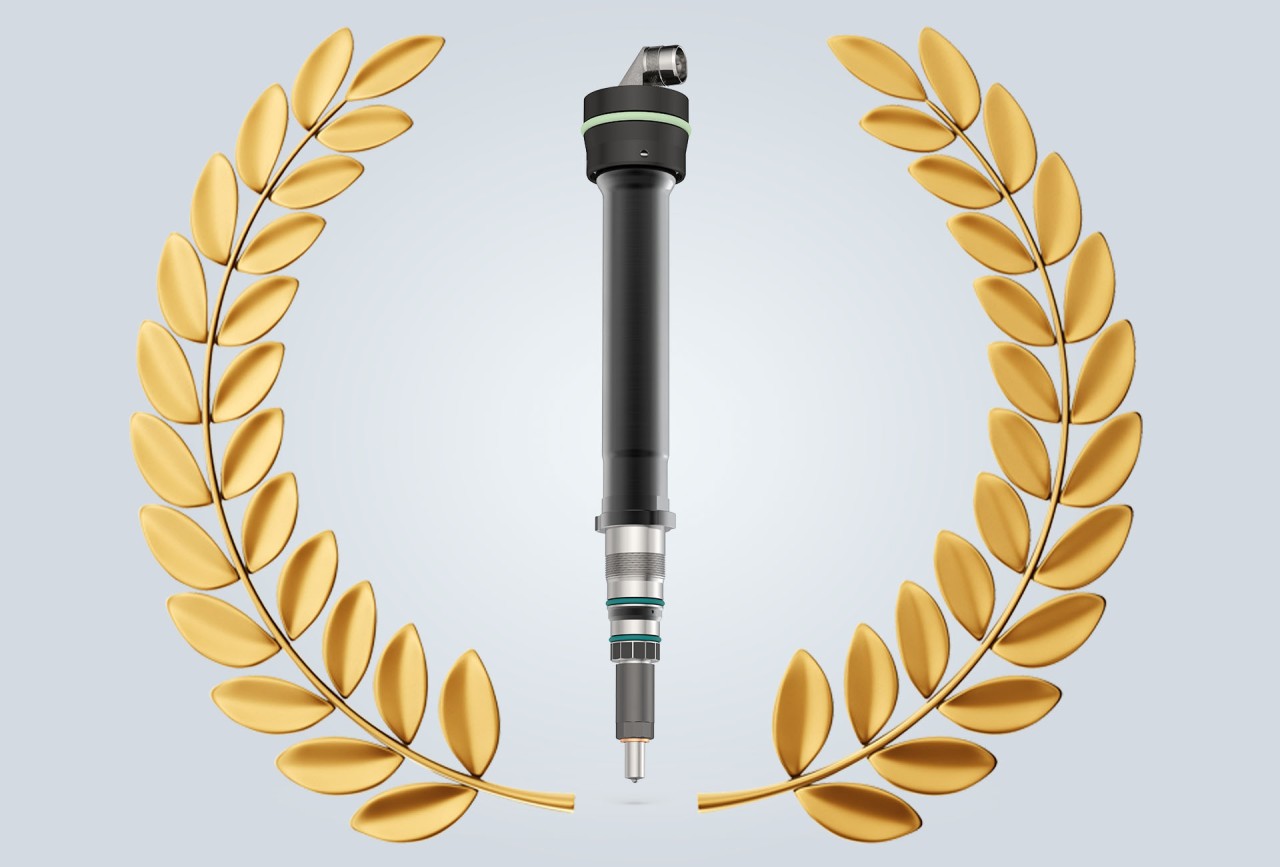
20,000 hours: Liebherr injectors excel in field test
Increase in performance of up to 25% - no problem for our LI3 injector. The common rail injector for large engines impresses in the field test with an above-average runtime of 20,000 hours when used in an Australian iron ore mine.
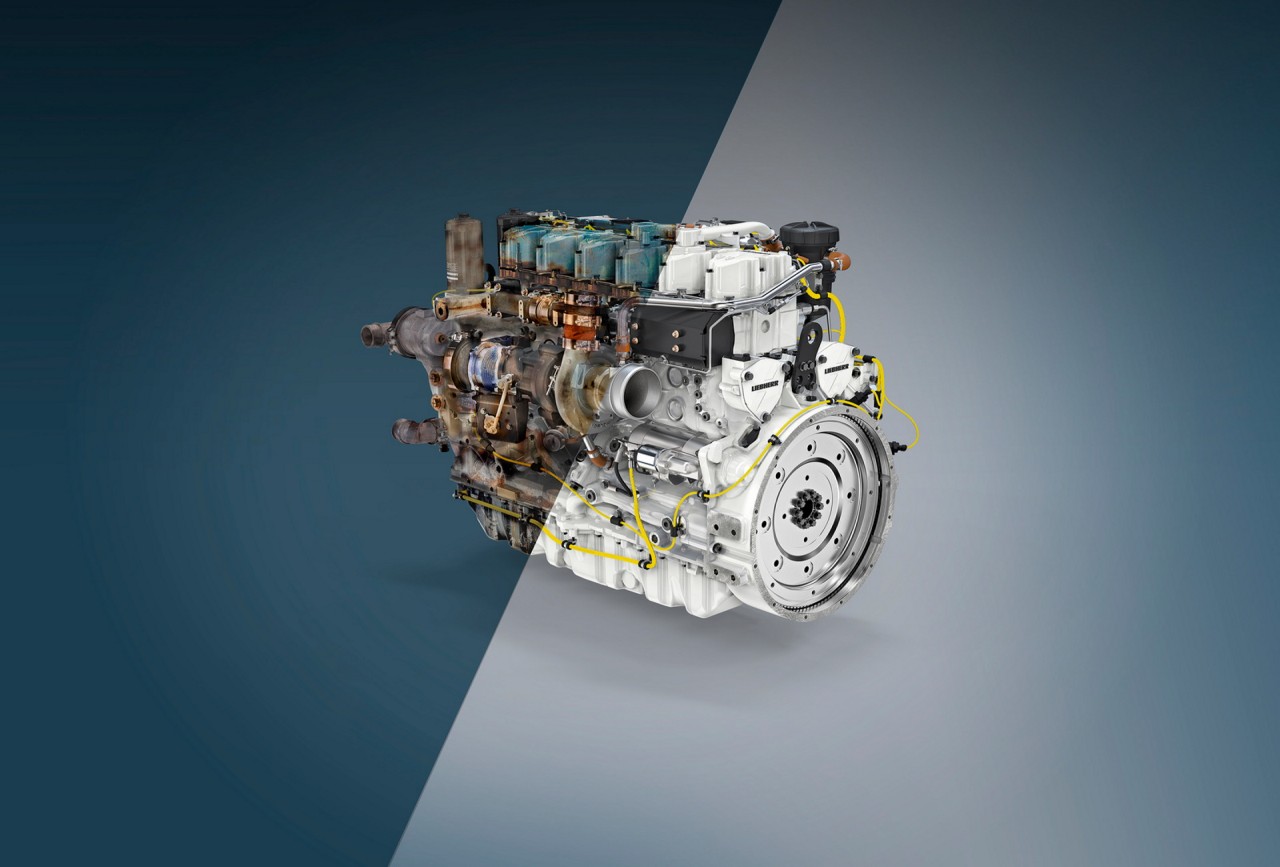
10,000 engines remanufactured
At our Reman facility in Ettlingen, a new milestone has been reached: We’ve recently surpassed the mark of 10,000 remanufactured engines. As compared to newly manufactured exchange engines, our customers have thus benefited from savings in the double-digit million-euro range without compromising quality. In addition, there are also remarkable environmental benefits worth mentioning.
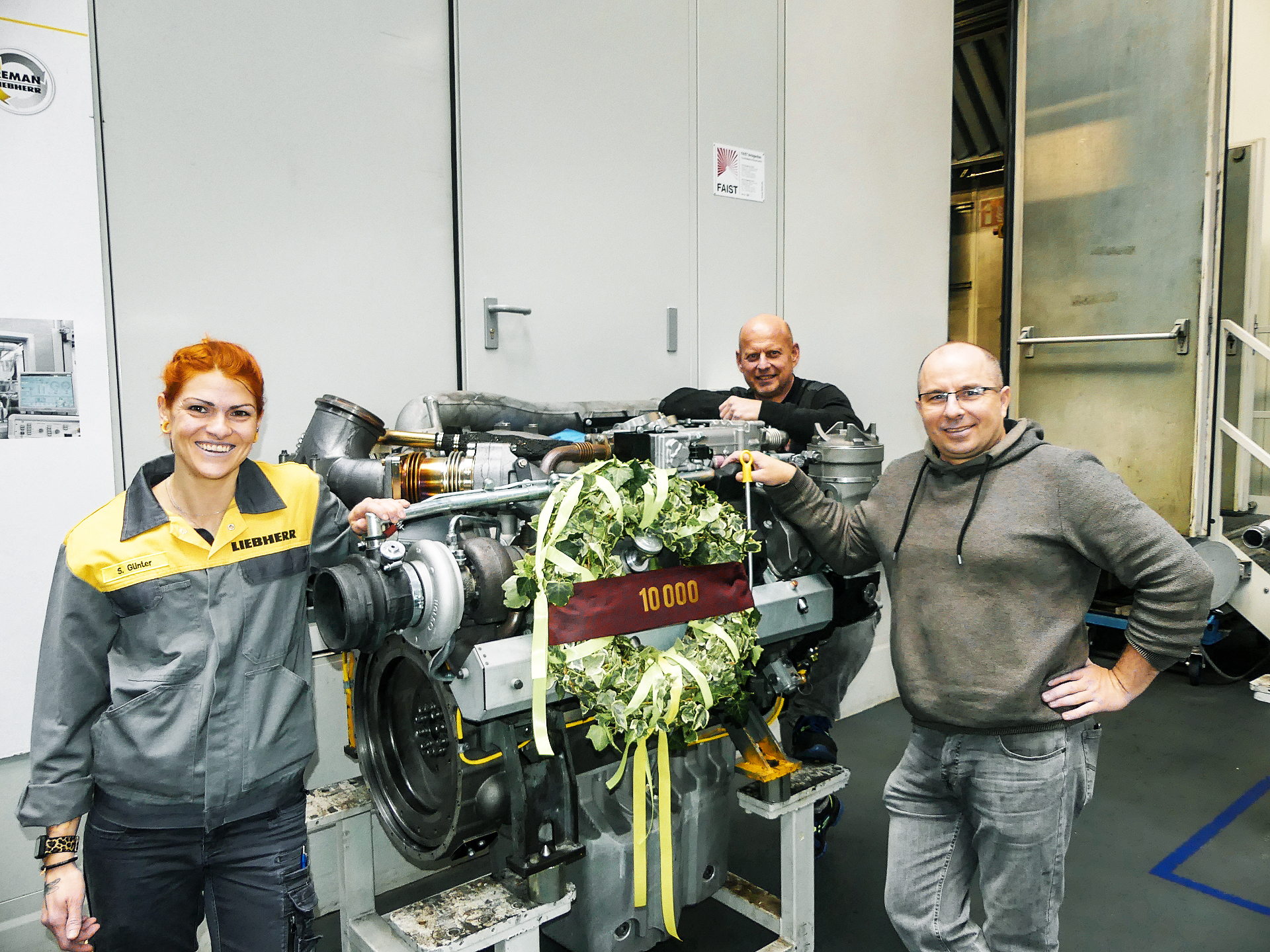
When reused, heavy parts do not have to be melt down again, which saves much energy. At the same time, the demand for primary raw materials decreases. Detailed studies have shown that we are able to reduce our CO2 footprint by 750 kg per engine. Extrapolated to 10,000 engines, this adds up to 7,500 t! This is equivalent to the amount of climate-relevant emissions emitted on over 1,500 flights from Frankfurt to Vancouver. We constantly expand and improve the Reman programme to make it even more efficient.
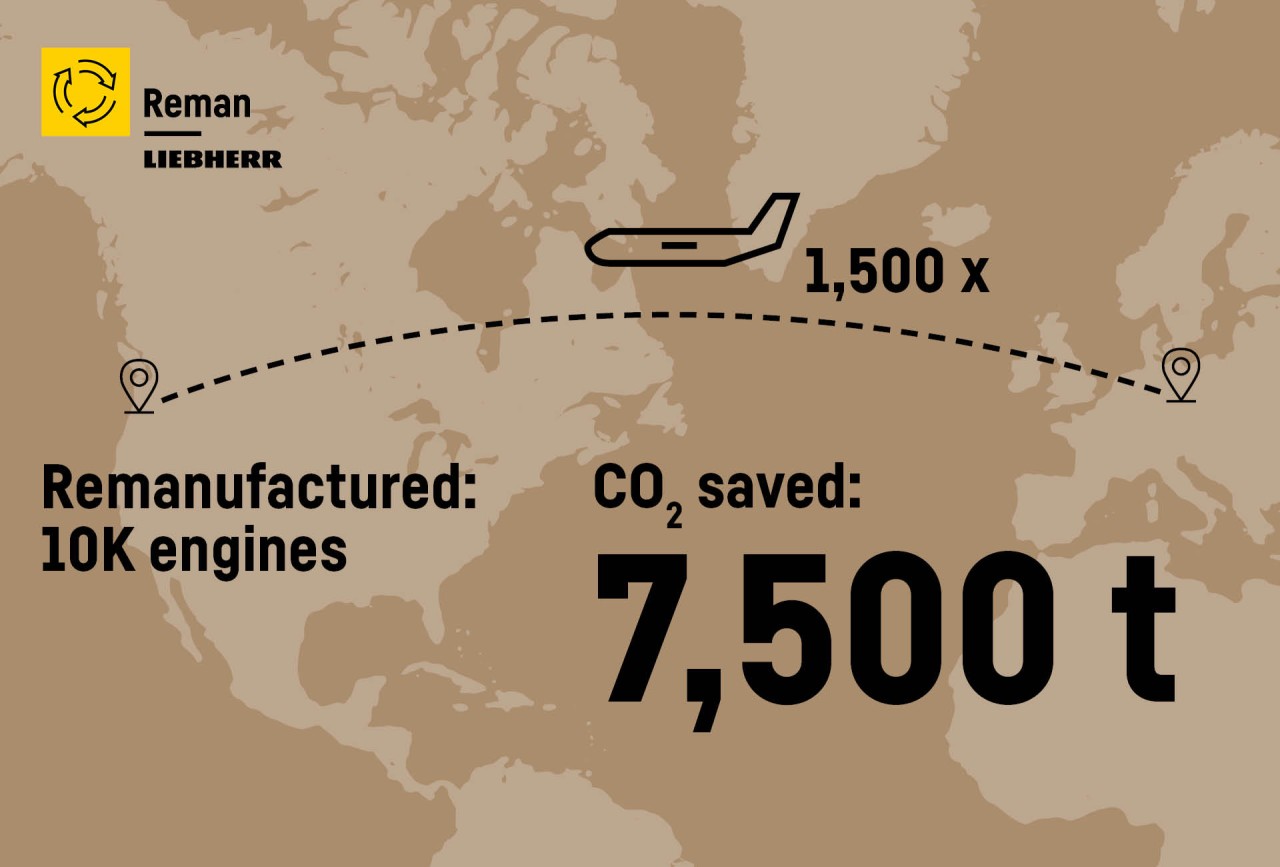
There it is - the 10,000th engine that we have refurbished in Ettlingen so far. Combustion engines have been part of our Reman portfolio for over fifteen years. These are used to power construction machinery, mobile and maritime cranes. The remanufactured gas engines, in turn, find there use in decentralised energy generation. Our customers benefit from cost savings and long-term availability of spare parts through remanufacturing; and the environment benefits from CO2 emission reduction:
Sign up now!
Stay up to date with our latest product highlights and innovative technologies.
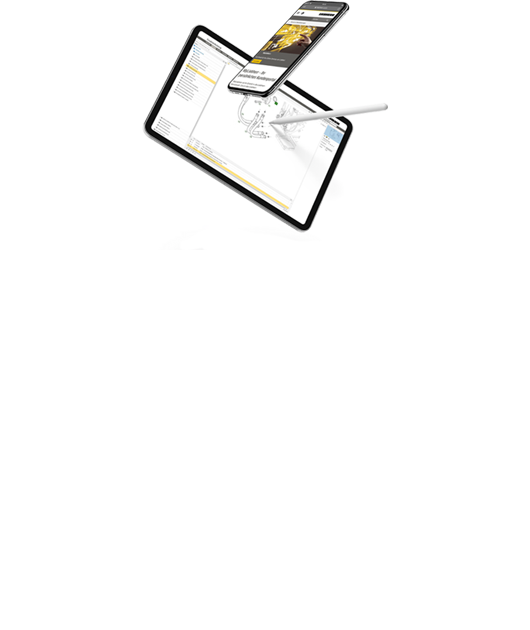
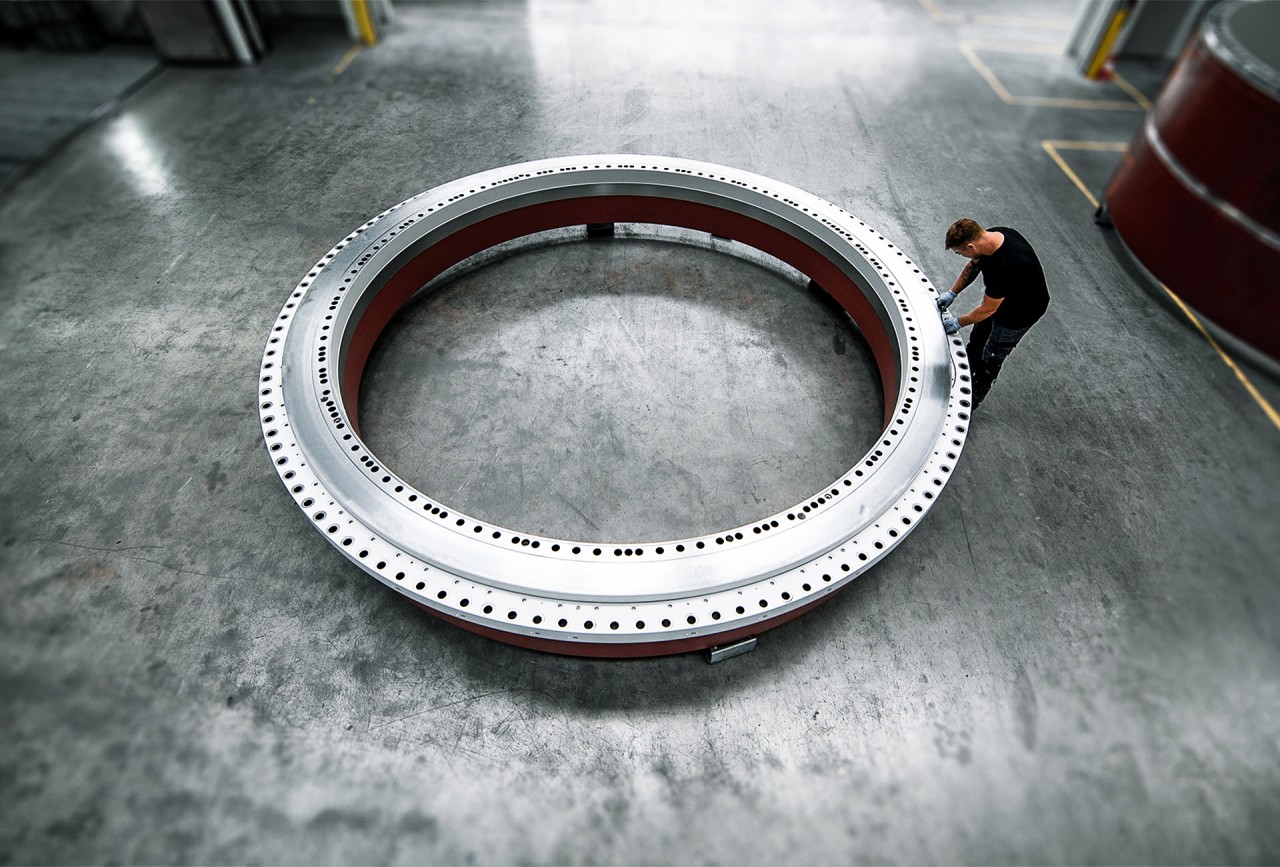
Slewing bearings for self-alignment of floating wind turbines
Harnessing wind power offshore: Our slewing bearings ensure self-alignment of Ming Yang’s floating wind turbine Nezzy². The triple-row roller bearings with a diameter of four metres function as a mooring system for the self-alignment of the offshore wind turbine. Exposed to the roughest conditions, such as seawater and fouling, their seal must therefore be even rougher: The special multiple stage sealing system designed for underwater or near-water environmental conditions saves resources and prolongs the lifetime of the bearing.
Excited about what is yet to come?
Join us this summer and be the first to know. We will be there with more news from our components world.
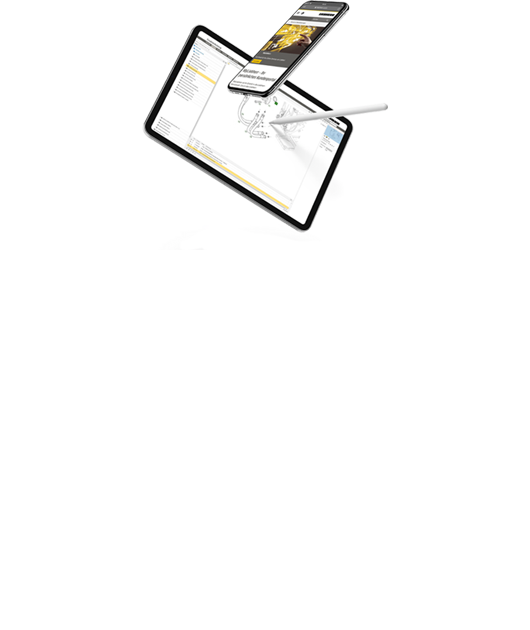