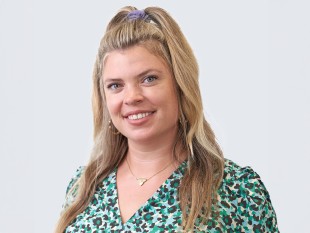
Lisa Kahlig
Marketing PR & Press
Liebherr-Werk Telfs GmbH
Hans-Liebherr-Straße 35
6410 Telfs
Austria
- Phone+43 5080 9614-13
The portfolio of international customer applications for telescopic handlers and crawler dozers is diverse. In line with its open-technology approach, Liebherr will be presenting at Intermat Liebherr a range of alternative engines for telescopic forklift trucks, including a battery-electric machine in the 7-metre class.
Liebherr telescopic handlers excel with application- and market-optimized drive concepts: Hydrogenated vegetable oil (HVO) as a low-emission counterpart or additive to fossil fuels, battery-electric drives and a hybrid drive consisting of a combustion engine and electric motor.
HVO is a synthetic, but sustainable fuel that is growing in importance at Liebherr. It is the first fuel available commercially that can be used with conventional combustion engines in an almost climate neutral manner. Its production is climate-neutral if electricity from renewable energy sources is used exclusively during production. In addition, it produces lower emissions in actual use than a machine running on fossil diesel fuel.
Due to the excellent compatibility with all engine components and the miscibility with fossil diesel, the barrier to entry or conversion is low for customers. It even is possible to switch back to fossil diesel during operation, for example, in the event of procurement bottlenecks. Basic processes at the end customer do not have to change either: The drive concept remains in place without loss of performance, there are no other maintenance steps and no additional technical training is required.
The local emission-free solution for the Liebherr telescopic handler is a modular high-voltage battery design paired with an electric drive, which can be scaled according to customer requirements and application, and is equipped with on-board charging electronics. 3/5 This drive is particularly suitable for indoor applications, such as recycling, and offers an impressive increase in driver comfort, low noise emissions and optimised vibration behaviour.
Due to the charging times, switch over to an electric machine requires certain organisational changes for the customer. But equally, this drive uses electricity, the most widely available source for self-generated primary energy and offers control and regulation advantages in use. This advantage also applies to the hybrid drive concept described below.
The third potential telescopic handler drive concept - a serial hybrid with "plug-in" - guarantees customers are not restricted by range and allows operation without a battery. Of the three systems presented, it has the highest overall efficiency and the ability to recuperate energy when braking and lowering the boom. This means fuel savings of more than 20 percent are achievable.
In the face of the constantly increasing pressures on time and costs, construction machines have to meet the highest demands, both in terms of speed and precision in operation, in order to win through. For this very reason, automatic machine control and operator assistance systems are being used ever more extensively to increase the productivity of operator and machine.
The intelligent assistance systems in generation 8 crawler dozers include three levels of driver support: Free Grade for active blade stabilisation during fine grading; Definition Grade for automatic blade positioning when creating simple 2D surfaces, 3D Grade for modelling complex terrain forms. These "3D grade" solutions use digital planning data to automatically control the machine equipment when removing or applying material. Using the latest technology, complex surfaces and exact planes can be produced swiftly and precisely.
Marketing PR & Press
Liebherr-Werk Telfs GmbH
Hans-Liebherr-Straße 35
6410 Telfs
Austria