02
Beyond State Lines
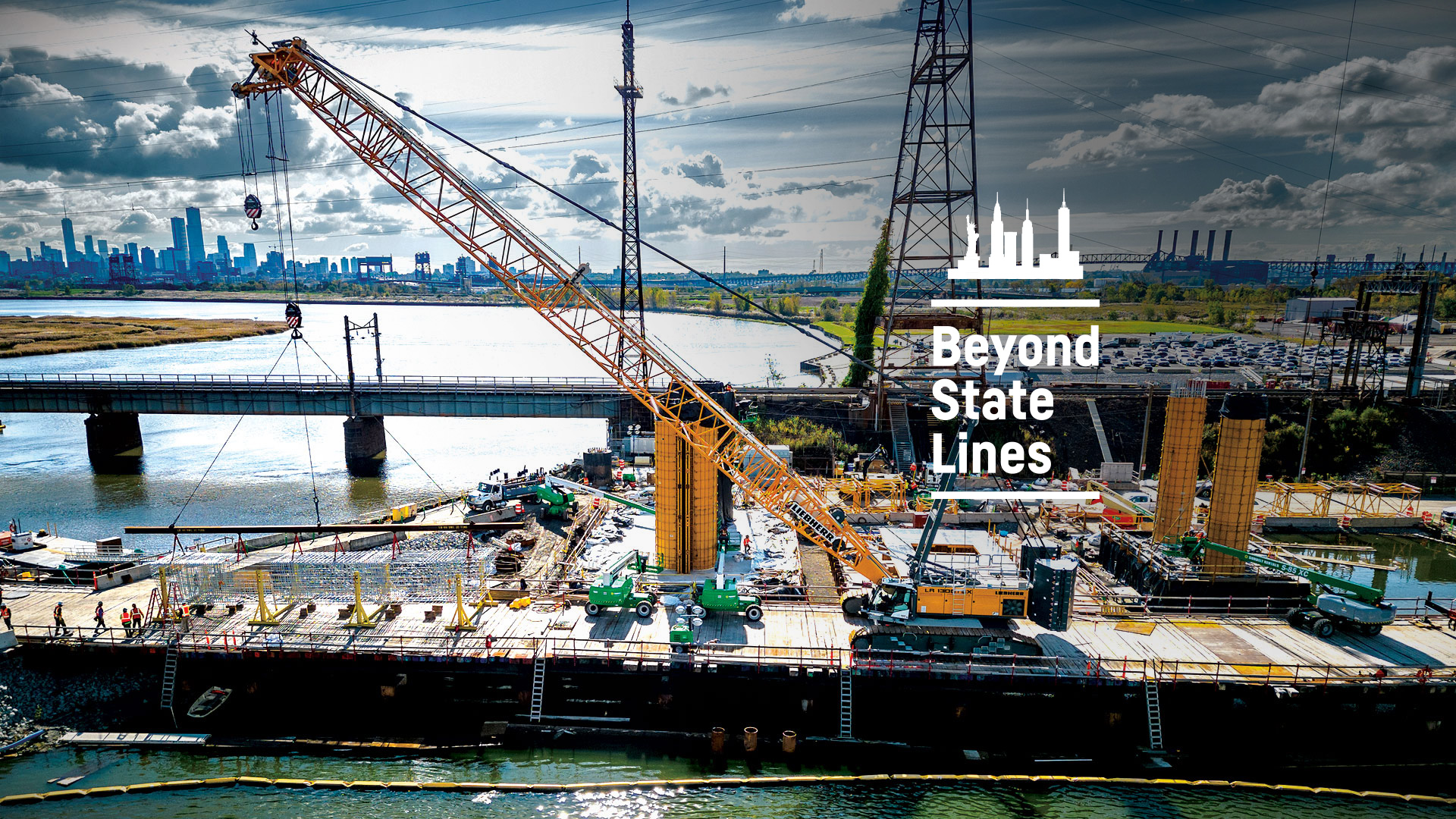
03
Partnership with Fortescue
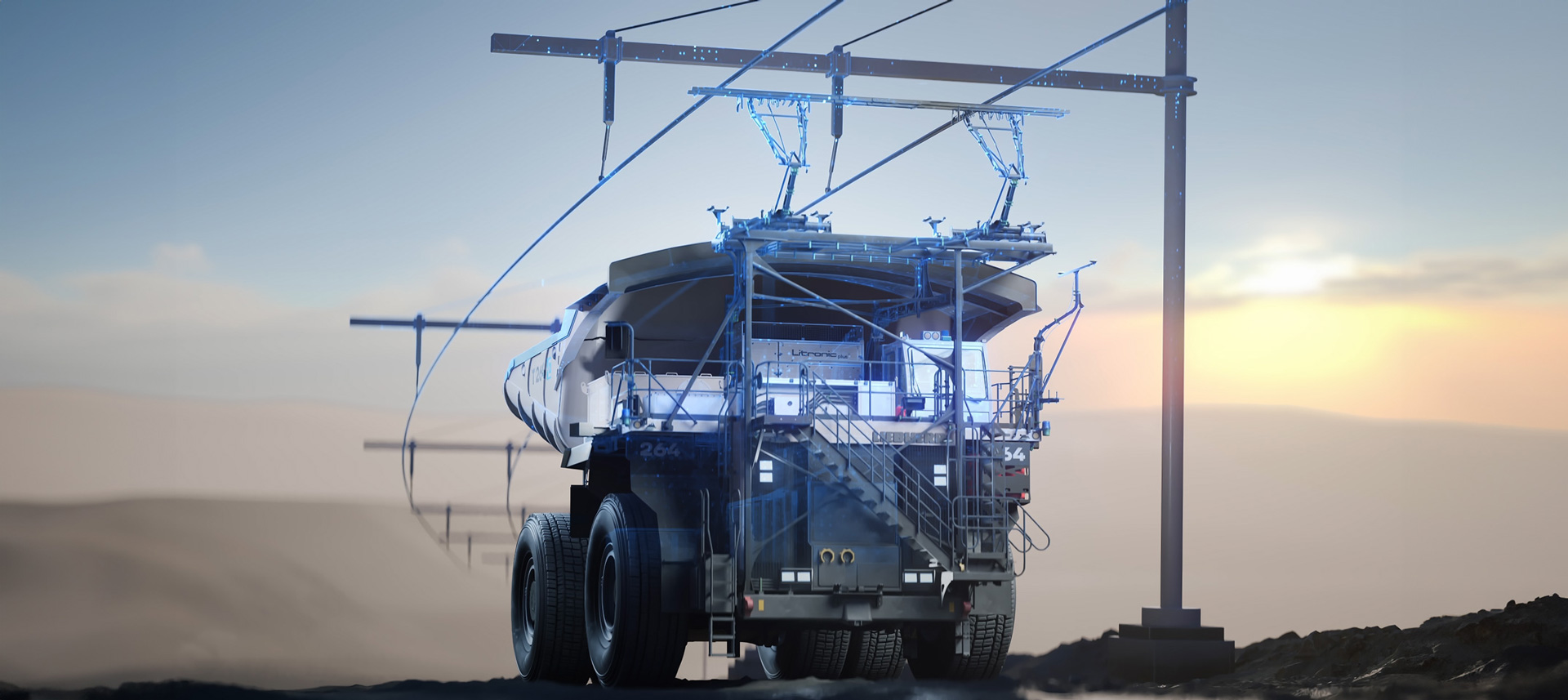
04
Used Equipment Marketplace
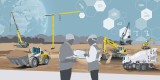
The Liebherr Group
For more than 75 years, Liebherr has stood for a large, continually developing range of sophisticated products and services. Exceptionally practical, seasoned and proven engineering as well as a consistent high quality level ensure customer benefit in all product areas.
Highlights from the Liebherr world
Other topics
- Used Equipment Marketplace
- Merchandising shop
- Sales and service