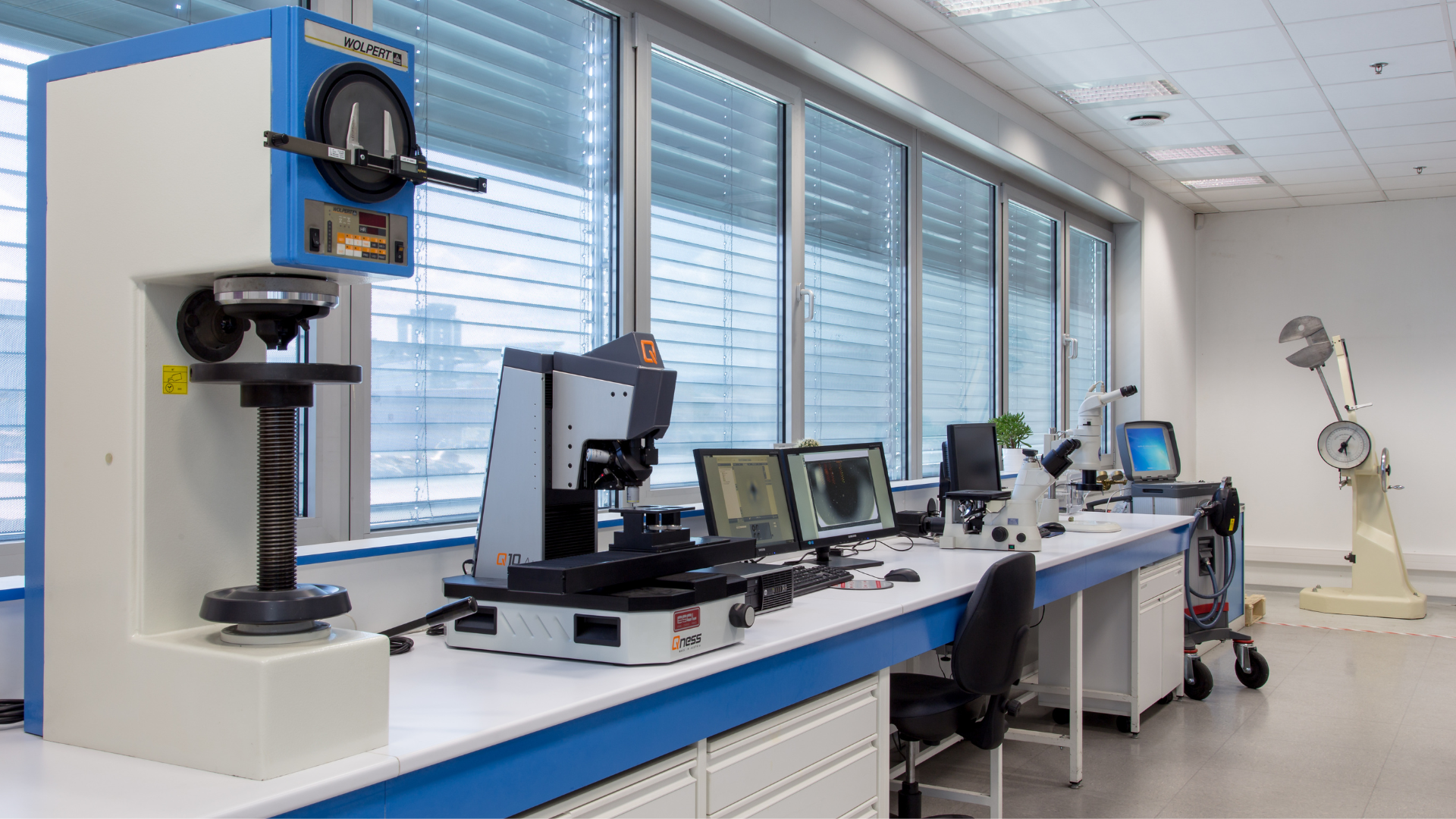
Only the best for Liebherr Mining
Liebherr-Mining’s Quality Lab is vital for ensuring product quality. Quality Lab uses its specialist expertise to help customers get the very best out of their Liebherr equipment and can perform the same assessments in their state-of-the-art lab that they carry out in mine sites all over the world!
One of Liebherr’s core values as a company is to provide the highest quality in everything that it does. To do that, Liebherr needs to ensure the quality of the parts used in its equipment, confirm that suppliers are matching the company’s quality expectations, and give first-class equipment advice and support services to customers wherever they are. At Liebherr Mining, an important resource for achieving this is its Quality Lab, which was founded in 2012.
Experts in their field
Each member of the Quality Lab team is exceptionally experienced. All seven members have advanced qualifications in a range of fields. There is one PhD in metallurgy among these remarkable individuals! And as well as these impressive credentials, each Quality Lab staff member has been certified according to international norms by all relevant official organisations.
“The work that we do within Quality Lab deals in minute details and highly technical information,” says Vanessa Gutierrez, Group Leader, Quality Lab, Liebherr-Mining Equipment, Colmar SAS. “As such, it is vital that each of our team members has a deep understanding of their domain so that no question goes unanswered.”
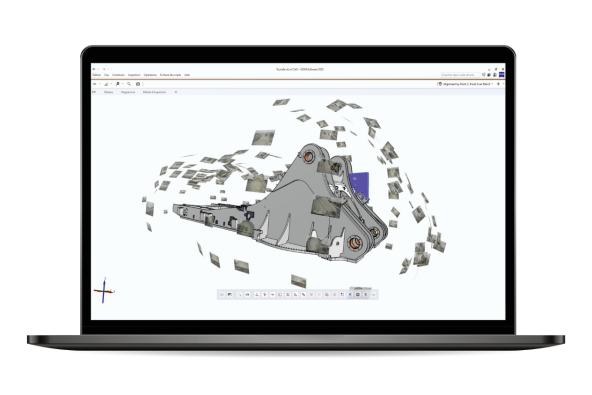
Quality Lab 3D measurements
Quality Lab has five core competencies that are used when helping customers understand and overcome challenges on site or when offering advice to suppliers and customers’ technical teams. These are welding, metallurgy, non-destructive testing – e.g., visual, ultrasonic, magnetic, and penetrant testing – 3D measurements, and surface finishing. The combination of these core competencies allows Quality Lab to take a granular approach to problem solving and quality control.
“After one of our customers’ excavators suffered some damage, we were asked to help them assess which parts and components from the machine could be reused,” says Gutierrez. “By taking 3D measurements of the excavator’s parts, we were able to compare these dimensions to those from Liebherr’s engineering department to see which ones could be kept, which required some refurbishment, and which parts needed to be written off. By providing this information to the customer, we were able to help them avoid purchasing all new parts for the machine.”
Complete customer focus
When customers need Quality Lab's help, they do not need to make any special trips to the Quality Lab facility, located at Liebherr’s excavator factory in Colmar, France. Rather, Quality Lab technicians pack up their testing and measurement equipment and meet customers where they are. Quality Lab has been set up to be completely mobile; all testing that can be completed at the Colmar facility can be undertaken off site, whether at the bottom of a mining pit or at one of our suppliers’ factories.
“Our purpose is to address component quality issues as quickly as possible. This means we don't rely on samples that need to be extracted from a machine and then sent away for testing. We bring the microscope to the machine, not the other way around,” explains Gutierrez.
Conditions on site can be a stark contrast to the controlled environment of a laboratory. Severe weather conditions, limited connectivity, and remote locations are just some of the challenges faced by technicians on a mine site. But these do not impact Quality Lab’s ability to do its job.
“We understand the constraints that customers face every day and so we work with onsite conditions, rather than asking customers to accommodate us and interrupt production,” says Gutierrez. “If customers are working in the rain, then so are we.”
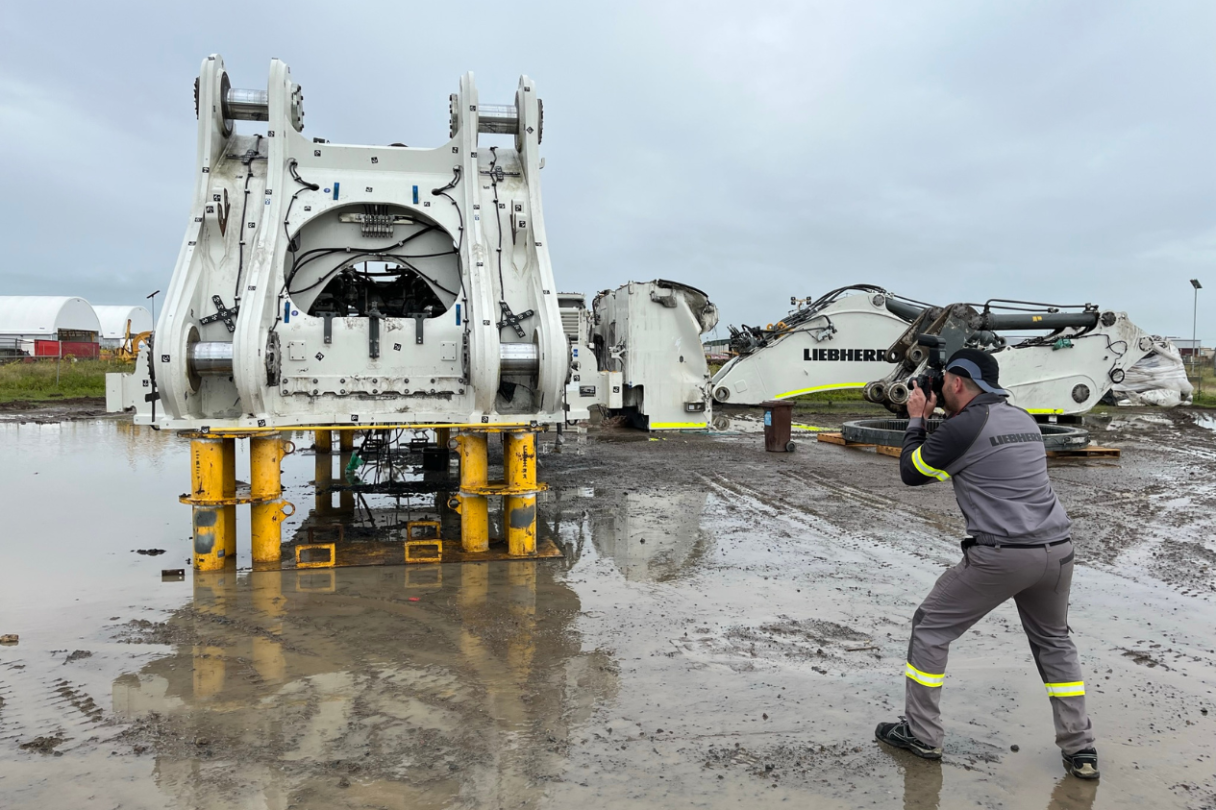
Member of the Quality Lab team preparing images that will be used to assess the status of an excavator component.
Despite the challenging conditions, mine sites operate as well-oiled machines. As productivity is one of the utmost concerns of mining companies, an unexpected maintenance issue can cost the mine time that they cannot afford to lose. This is where Liebherr Mining’s Quality Lab can provide invaluable support.
“Our team can be flexible and adjust job priorities as needed as we only work with Liebherr equipment,” says Gutierrez. “This means we don’t have to juggle the priorities of multiple OEMs. So, if a customer experiences an urgent machine issue, we are able to make sure that this customer receives timely support from Quality Lab to minimise downtime as much as possible.”
The tasks that Quality Lab performs for customers can differ based on the country in which the work is occurring. Different countries have different safety protocols, different resources available, and can have customers of different sizes – all of which can impact the type of jobs Quality Lab become involved in.
Shared knowledge
Not only are the members of the Quality Lab team incredibly skilled in their chosen fields, but they also have access to critical information that is likely not available to customers or external suppliers such as a third-party lab. Being able to speak with Liebherr’s engineering department, review Liebherr’s schematics, and understand how suppliers build their parts can give Quality Lab more context about what might be causing equipment issues and therefore provide more avenues to explore during the problem-solving process.
But Quality Lab doesn’t keep all this invaluable knowledge itself! Instead, the team uses its expertise and OEM-training to offer detailed, accurate, and reliable advice to customers and suppliers that can help improve equipment reliability. This in turn helps suppliers to improve the parts that Liebherr uses in its products while also optimising customers’ onsite maintenance and repair practices.
“We were asked to assist a customer with the replacement of a front bearing for an R 9350. The excavator’s stick had already achieved its expected service life and so the replacement was like a kind of remanufacturing to move the machine into its second life,” explains Gutierrez. “While we were there, we were able to provide recommendations to the customer on which onsite personnel would be best equipped for certain tasks in order to reduce maintenance time. Further, we were able to help the customer identify gaps in the knowledge of onsite personnel and how to address these to save time and optimise the maintenance process.”
The degree to which Quality Lab is involved in the repair process with customers is entirely dependent on the customers’ needs. In some cases, the team may be asked to evaluate whether repairs or replacement would the most effective course of action in certain scenarios. At other times, the team may be called upon to help establish onsite repair procedures by providing working instructions to the responsible personnel. There can also be situations where Quality Lab becomes involved in the repairs themselves and checks steps taken, provides training, and/or validates the repairs performed.
Quality Lab is future proof
Each year, Quality Lab reviews its stock of state-of-the-art equipment. As the tasks Quality Lab participates in can change to reflect demand, the team may need to add new pieces of equipment in order to provide the best possible service. The most recent addition to the lab is a salt spray chamber that can help the team check anti-corrosion coatings. It works by subjecting a test specimen to a solution of sodium chloride and water that mimics sea water in order to assess the durability of anti-corrosion coatings. Testing parts and components in this way helps to ensure that Liebherr’s equipment continues to align with changes to safety regulations in different regions around the world.