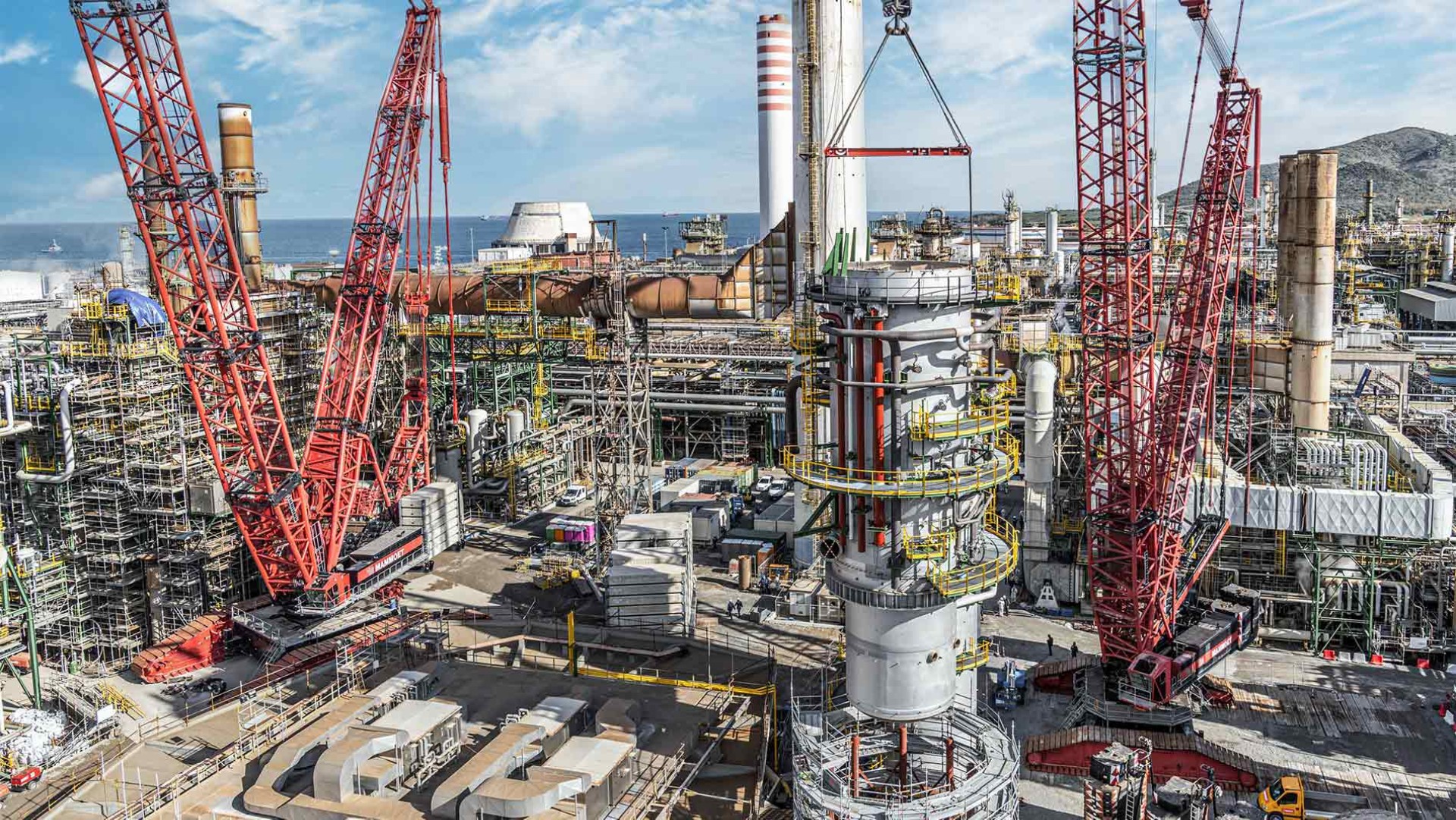
7 minutes | magazine 02/2022
Two power packs on Sardinia
Reports of what at the time was the newly discovered coronavirus first started to appear in the news in January 2020. At around the same time, three ships tied up against the quay in the port of Cagliari, the largest town on the Italian Mediterranean island of Sardinia.
Pandemic surprises Mammoet team on Sardinia
Their holds and decks contained crane materials and equipment from Dutch company Mammoet, specialist in engineered heavy lifting and logistics. They also had two of the very largest Liebherr crawler cranes on board. They had been sent to carry out extensive refurbishment work at a refinery. Just a few weeks later, the Italian authorities locked down large epicentres of coronavirus outbreaks in the country with many production sites being closed. For eight Mammoet employees in Sardinia, months of hardship began with a lot of work and no replacement. Substitutes were not allowed to travel to the island.
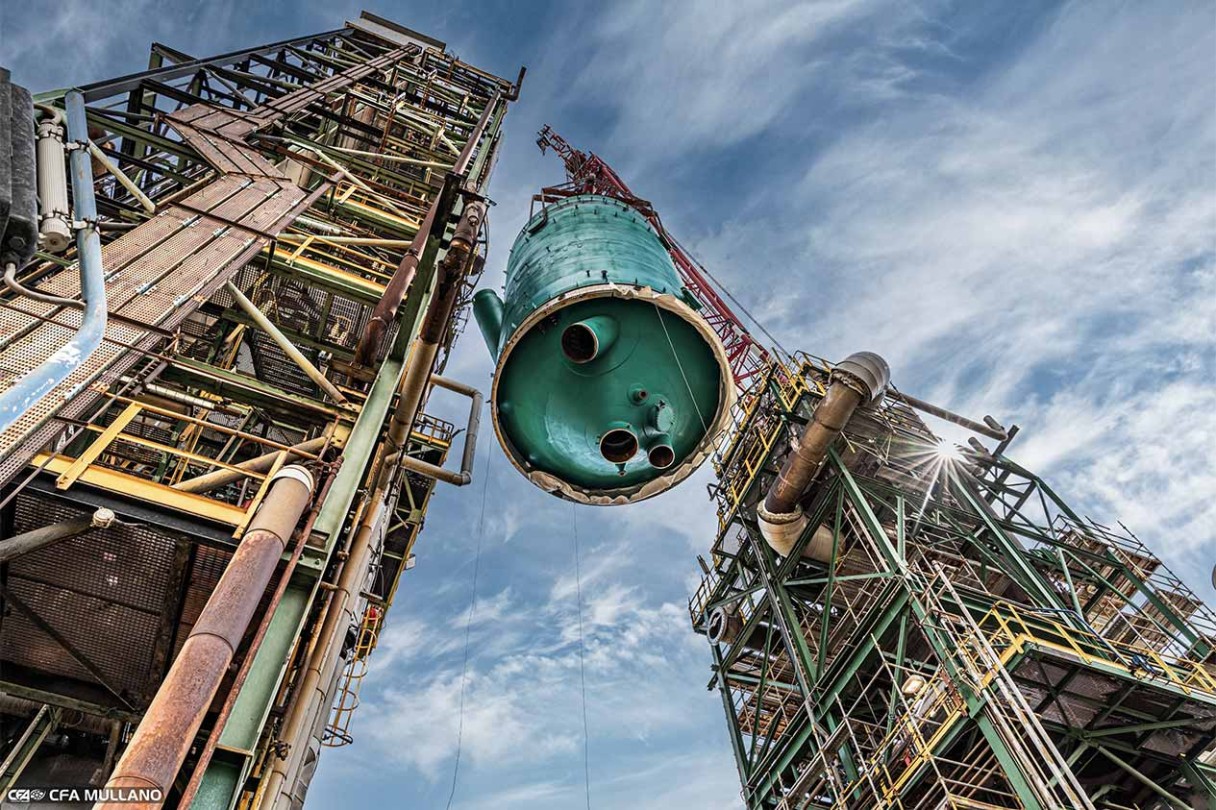
Centimetre precision - The FCC regenerator weighing over 500 tonnes was transported past existing systems with great precision.
Naturally, Simone Agostinetto, the Mammoet Site Project Manager, and his seven colleagues had no idea at the time that their professional visit to the island would ultimately last for the entire project period of over six months. But the very strict travel restrictions that were implemented quickly throughout Italy, including on Sardinia, meant that the crew of crane operators and personnel for the SPMTs (self propelled modular transporters) could be neither strengthened nor relieved. This meant that the small team from the heavy lift contractor was left completely on its own to tackle the impending job with their extensive, massive equipment during the shut-down of the petrochemical plant. In addition to a Liebherr LR 11350, the team also had one of the very largest Liebherr crawler cranes with them – an LR 13000.
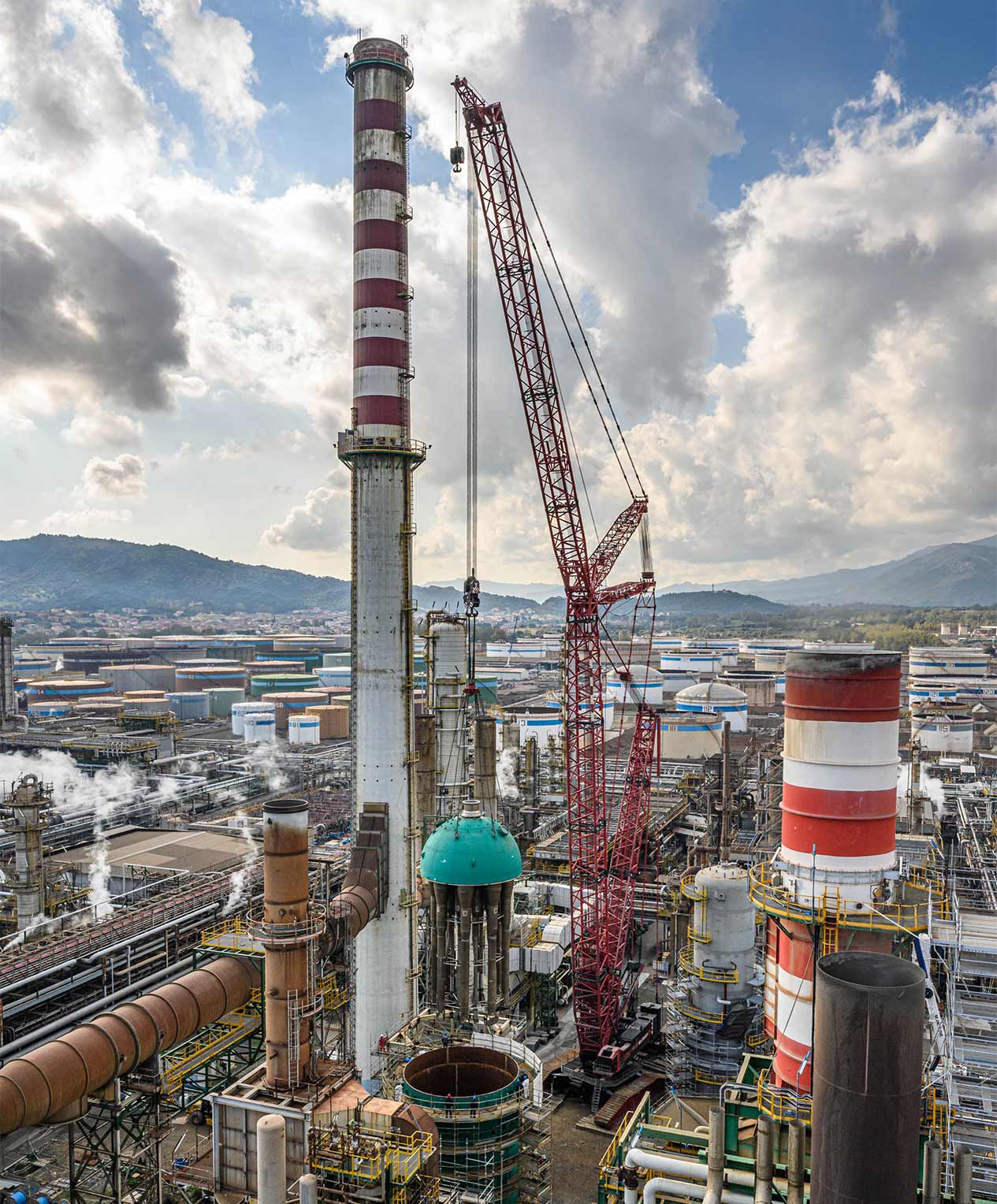
No claustrophobia - The restricted freedom of movement is shown quite clearly in this photograph of the LR 11350.
To date, Liebherr has built six of these enormous cranes and delivered them to its customers. The first one, shown here in the photographs, was handed over to the Dutch company almost exactly ten years ago. Since then, the crane has been used in major projects all over the world. For example, it was in action in Dubai building the largest Ferris wheel in the world. Mammoet has been an important partner for us for decades and also designs and manufactures special large cranes itself with enormous dimensions for its own applications.
But let’s get back to the island. The two Liebherr crawler cranes were the ideal tools for the work required on the refinery site on Sardinia’s southern coast. Many of the plant components and even the large reactors and columns had to be moved to carry out the factory refurbishment. The largest load for the LR 13000 was a so-called FCC regenerator. The abbreviation FCC stands for “fluid catalytic cracking” which is a material conversion process in the crude oil-processing industry. To hoist this colossal component, the 3,000 tonne crawler crane had to be rigged for the gross load case of a massive 695.5 tonnes at an enormous radius of 65 metres, including a reasonable safety reserve. The manoeuvre with the regenerator on the hook was a massive challenge for the entire team, because it had to pass through extremely constricted areas. In some cases, there was less than one metre between the load and the plant.

Dimensions made visible - Massive counterweights ensure adequate stability. The LR 13000 was fitted with a total of 2,050 tonnes of ballast for hoisting the heaviest components.
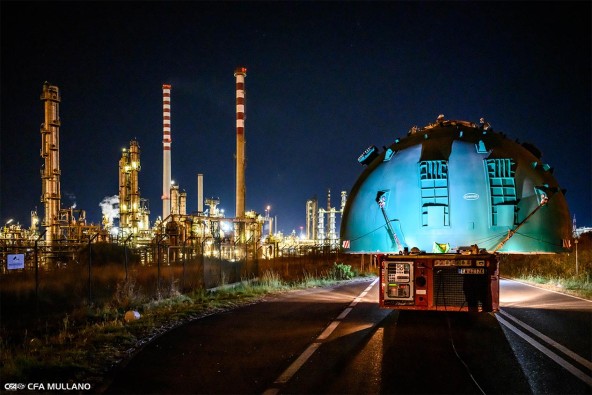
Piggyback - The small transport crew had to move enormous loads with their SPMTs, sometimes even during the night.
But it was not just the gigantic loads that posed a major challenge to the Mammoet team, but also the storage areas and movement areas for the cranes themselves within the extraordinarily constricted terrain surrounded by petrochemical systems. “It was for precisely these jobs that we equipped the LR 13000 with what are known as B0 table, a version of load charts for crane operations with suspended ballast”, says Jens Könneker, Product Manager for Crawler Cranes here in Ehingen. “The net weight of the derrick drawing cylinder which remains on the counter boom and the draw bars is taken into account, however. Even though they only amount to 50 tonnes, we can use them as counterweights.” This means that the crane can be used on constricted sites or for working with a small radius very flexibly without having to restack ballast.
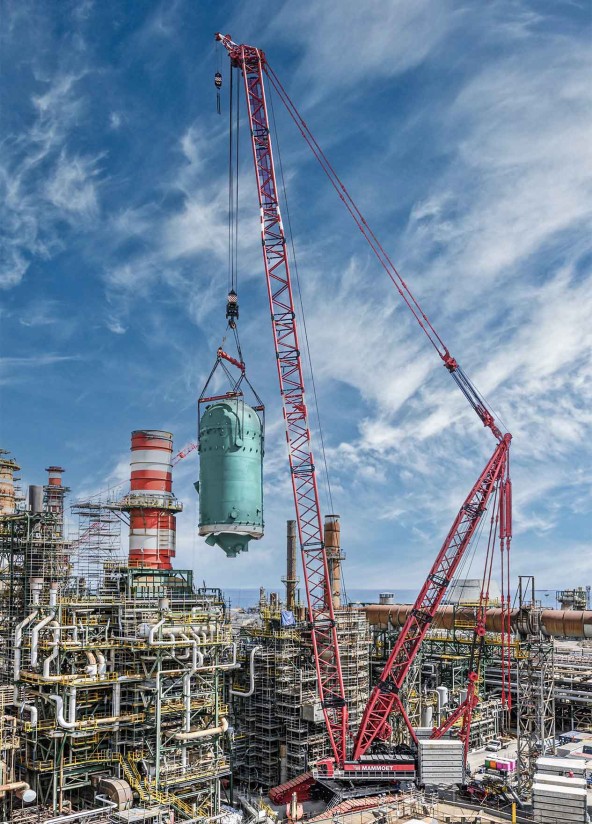
Smart in constricted spaces - The LR 13000 can put down the suspended ballast and operate in very tight spaces when it is used with a small radius. The 50 tonne weight of the derrick drawing cylinder which remains on the counter boom and draw bars are used as ballast and included in the calculations. This was an important feature for operating in the constricted space between the refinery systems on Sardinia.
The Mammoet team took full advantage of this set-up version on Sardinia. Simone Agostinetto: “The ballast pallet only had a few centimetres of space to the side. That meant we were forced to pick up the regenerator with such a short radius that the LR 13000 could initially handle the load without any suspended ballast. We then docked the suspended ballast into place when the crawler crane was in position to unload the component. It worked really well.”
In any event, Agostinetto and his team delivered fantastic work on Sardinia. In the summer, after spending six months in island quarantine, he and his crew were finally able to pack their bags. Mission accomplished! When asked how the eight-man team managed to complete such an enormous task with no reinforcements and no relief, Project Manager Agostinetto commented: “The team was very experienced and flexible.” And he continued: “Eight highly motivated men can achieve a lot if they get some food and coffee.”
This article was published in the UpLoad magazine 02 | 2022.