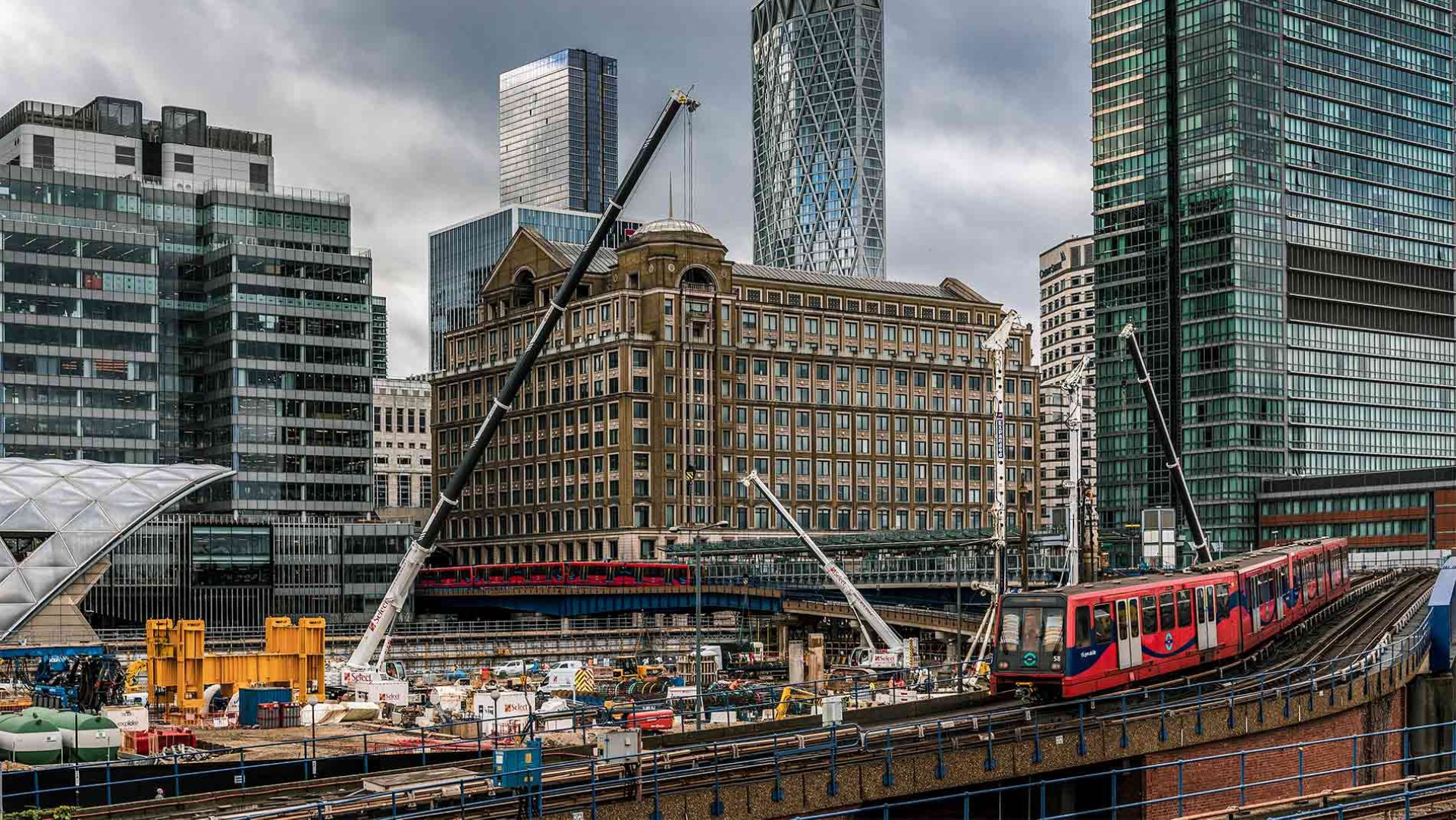
16 minutes - magazine 02 | 2023
Very busy
We have been manufacturing crawler cranes with telescopic booms here in Ehingen since 2005. In its early years, this crane type was overshadowed by our traditional mobile and crawler cranes.
A crane for (nearly) all cases – LTR cranes are working continuously on major British projects
But since then, the popularity of these highly flexible and compact LTR cranes has increased enormously. This is underlined by a current look at the British capital. On numerous and extensive construction sites – our cover picture shows construction machinery in the centre of Londonʼs “Canary Wharf” business district – Liebherr cranes, which are mobile even with a load, are increasingly common sights.
Liebherrʼs telescopic crawler cranes are not just rolling over the rubble on the huge Canary Wharf construction site in Londonʼs Docklands, where a fashionable shopping and residential area is being built on more than three hectares next to gigantic skyscrapers. The machines are also in great demand on the construction sites for “HS2”, currently the largest railway infrastructure project in Great Britain. Our compact lifting units are performing numerous important tasks there, especially when it's not just about lifting, but also about transporting materials on the construction sites.
HS2 – a succinct acronym which stands for “High Speed 2” and is the name given to the ambitious British endeavour to cut rail journey times from London to Birmingham by almost half by the end of the decade, and later further north to Leeds and Manchester. Trains that can reach speed of 225 miles per hour (around 360 kilometres per hour) are required for this, as are new, efficient routes, junctions and stations in the metropolisʼ underground. We visited three interesting HS2 construction sites and saw a number of telescopic crawler cranes in use there.
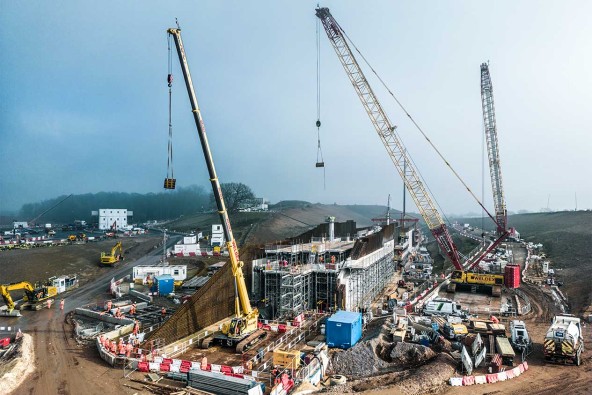
At the west portal of the future Copthall Tunnel, an LTR 1040 delivers material to the construction site. Two crawler cranes from Liebherrʼs production site in Nenzing (Austria) accompany the emerging structure.
250,000 passengers daily
So letʼs get one thing straight right from the start – the dimensions here are enormous. The gigantic construction sites for this project demand great respect and even greater walking distances from visitors. In future, the largest railway station ever built in Great Britain will be called “Old Oak Common”. For the past six years, it has been carved and built both into and on the ground in the west of the city. The construction site stretches for well over a kilometre. Fourteen above-ground and underground platforms will one day handle 250,000 passengers per day in the 850 metre station concourse. A considerable number of construction machines are at work at this giant hub for the HS2 project. It is also where we meet Amy Jacobs, a crane driver from Select Plant Hire Ltd. The young woman sits in the cab of her LTR 1100 and actually has very little time to chat.
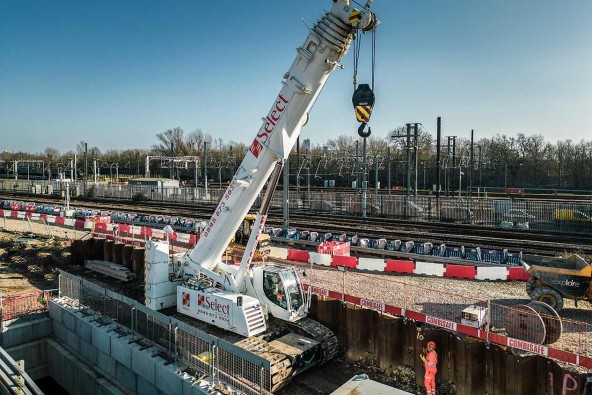
Making itself thin - To navigate a narrow passage, Selectʼs LTR 1100 has set its crawler travel gear to narrow track – a valuable skill when navigating construction sites.
“At the moment we have to move a lot of material and equipment to the lower level,” she explains, lowering the large concrete bucket on the hook block of her machine. “Other LTR cranes are being used for formwork or concrete work here,” Amy says. Huge quantities of equipment and building materials need to be moved underground to where, at a depth of 14 metres, the platforms for the highspeed trains are currently being cast. They will be just under half a kilometre long. “Especially on this expansive construction site, my crawler crane has to cover a lot of distance. Either to transport material or if there is a job waiting for me elsewhere,” Amy explains. “But it works really well – the machine is easy to control and very easy to drive.” No sooner said than done – her LTR 1100 is immediately requested on the opposite side. Because she has to pass through a narrow passage on the way there, Amy sets the crawler travel gear to a narrow position, reducing the craneʼs width to just 3.5 metres. Now 155 centimetres “slimmer” than before, it rolls away towards the next job.
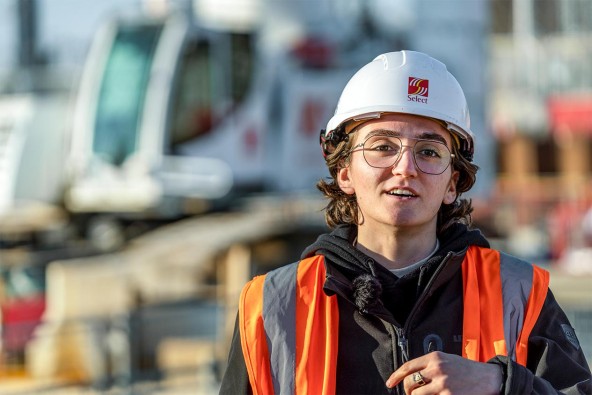
“I get exactly what I want from my crane...” is how Amy Jacobs describes the handling of her telescopic boom crawler crane. “Sensitive response, pleasant to operate and better to drive than any of my previous cranes.”
A construction site of extremes
Less than two kilometres away, another LTR 1100 also has a load on its hook, which it lowers into a huge shaft. At a depth of 20 metres, a team of orange-clad workers need a compressor. It only takes minutes for the mobile tele-crawler to drive up to the concrete edge with the tool and lower it down to the waiting men. This black-painted crawler crane belongs to Hawks Crane Hire Ltd and is also hard at work for High Speed 2. Different construction site, same massive proportions. Or at least thatʼs what Elliot Hawkins, company boss and the craneʼs owner, assumes: “The Victoria Road Crossover Box, where we are now standing, is, as far as I know, the largest HS2 construction site as far as manhole work is concerned,” Hawkins tells us. “Five really huge holes have been excavated in the ground here. Several tunnel boring machines are drilling through the London underground and will arrive here.”
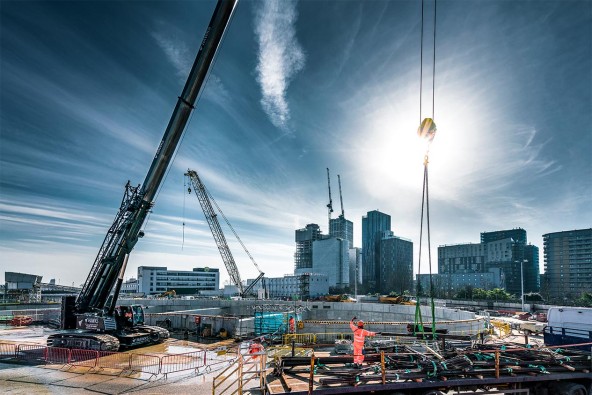
Material handling - Unloading incoming deliveries and feeding the site with material below ground – these are the main tasks of Hawks Crane Hire Ltdʼs LTR 1100 during construction of the Victoria Road Crossover Box.
The underground box structure, which will later be 130 metres long, will house a complex switch system, among other things. It allows incoming and outgoing trains from the station mentioned above to switch between tracks. Hawkins is using an LR 1300 SX lattice boom crawler crane to provide sufficient lifting power, as well as an LTR 1100 to ensure a high degree of flexibility while working around the enormous hole. “The LTR, with its 52 metre telescopic boom, can quickly serve all locations on the construction site to a sufficient depth from the edge. It is being used, among other things, for concrete construction and to transport formwork or reinforcement bars. The craneʼs extremely short set-up times, as well as its ability to travel with a load attached, ensure speed and efficiency on large infrastructure construction sites like this,” explains Hawkins.
Valuable feature: Pick & Carry
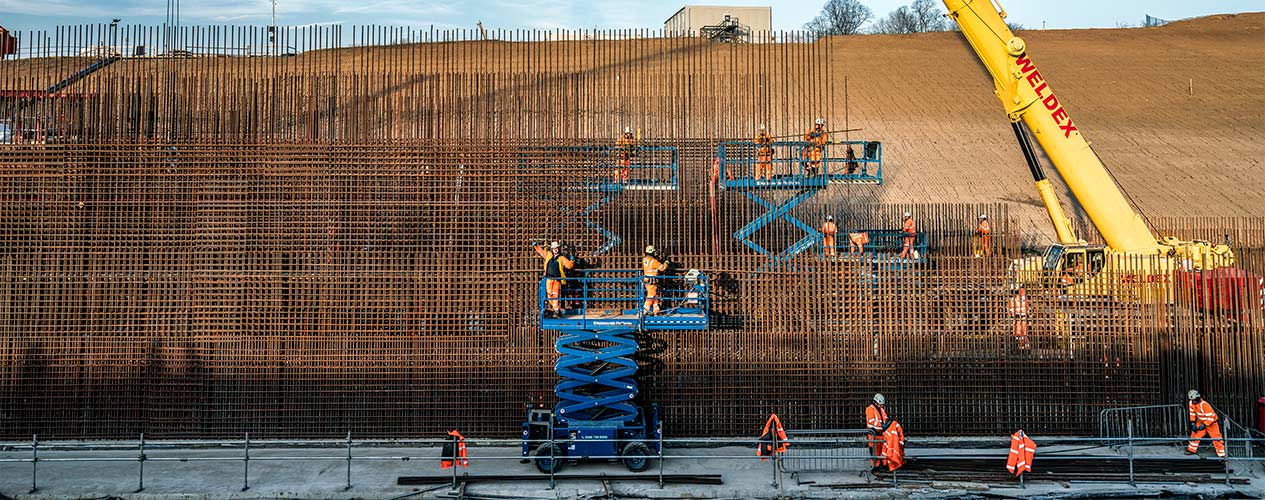
Behind the iron carpet the LTR 1220 telescopic crawler crane from Scottish crane contractor Weldex shimmers through the rust-coloured ironwork. The mobile powerhouse is supporting the reinforcement work during the construction of the Copthall Tunnel. One of the steel fixers takes the opportunity to pose for our camera.
Mark Hollet, Operations Director at Weldex, Britainʼs largest, global crawler crane contractor, has a similar view of another hotspot for the high-speed rail project. “Due to the flexibility of their telescopic booms and their ability to transport material, weʼre using three LTR machines on the Copthall Tunnel site.” Here near Uxbridge, on the western edge of the London metropolitan region, the Scottish crane experts have a total of five Liebherr machines in action. To manage the heavy loads, there are also two lattice boom crawler cranes from our sister plant in Nenzing, Austria, at the mobile construction site. An 880 metre long tunnel structure is being built here using the cut-and-cover method. After completion, the whole thing will be filled in again and covered with greenery.
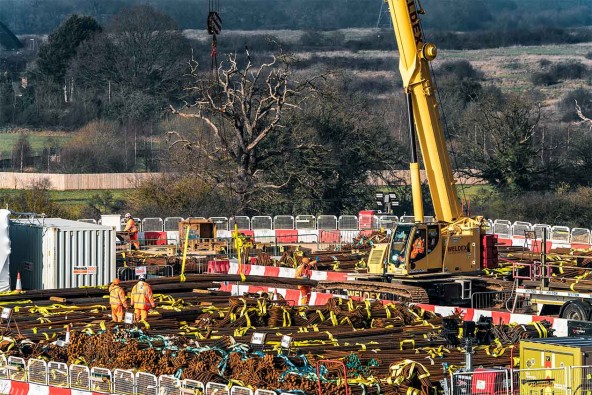
Storage yard logistics specialist - An LTR 1060 from Weldex ensures efficiency and order among the stacks of rebar.
The three telescopic crawler cranes are spread over the hilly area. One LTR 1060 exclusively handles the incoming construction material in the huge storage yard at the tunnel construction site and busily rolls back and forth between seemingly endless stacks of iron reinforcing rods. Two other units, an LTR 1040 and an LTR 1220, are directly involved in the construction of the tunnel. The large telecrawler is almost invisible between all the walls of rebar. It handles the supplies for the numerous steel fixers who must weave the metal rods into reinforcements for the nascent structureʼs walls. Again and again, the machineʼs crawler carriers start moving. Hoisting a lifting platform out or letting steel in – all the while being driven to wherever it is needed. The slats of its caterpillar tracks are covered by thick plastic plates. This protects the surface.
The reinforcement work here is scheduled to be finished in two years. Until then, the Liebherr crawler cranes from Weldex will remain in service. It is estimated that it will be another ten years before the first trains rush through the Copthall Tunnel and enter Old Oak Common Railway Station through the Victoria Road Crossover Box. In the 2040s, links to cities in the north of England will be built and Great Britainʼs “High-Speed 2” railway line will finally be a reality.
… follow-up!
There is a lot happening in the British capital and Greater London in terms of mega infrastructure projects. Particularly noteworthy is the fact that our crawler cranes with telescopic booms are being used more and more frequently on these large construction sites. Why are Liebherrʼs LTR machines so suitable for working on construction sites of this kind? This is explained to us by two people who ought to know: Mark Hollett, 20 years in the business and Operations Director at Scottish crawler crane contractor Weldex, and Elliot Hawkins, CEO and founder of Hawks Crane Hire Ltd. Both men are currently sending their Liebherr machines to construction sites that are pushing ahead at full speed with the UKʼs High Speed 2 (HS2) rail project. And both companies specialise in a niche sector of the crane market, namely crawler cranes.
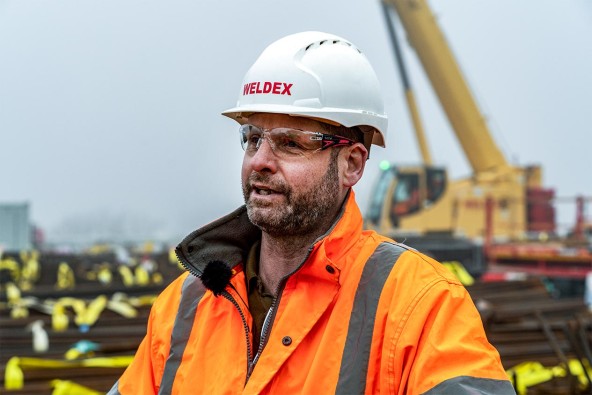
Mark Hollett - Operations Director at Weldex
What equipment from your fleet do you have in use here on the extensive Copthall Tunnel construction site?
Mark Hollett: Since low-emission construction vehicles which meet the requirements of exhaust emission level 4 or 5 are specified for all HS2 construction sites, we naturally use our newer cranes for these jobs. There are currently five on site – all from Liebherr. We use the LR 1300 SX lattice boom crawler cranes and an LR 1250 here because of the required radii and lifting capacities. Three crawler cranes with telescopic booms are also in use across the site – an LTR 1220 and an LTR 1040 directly at the tunnel construction site, as well as an LTR 1060, which is used in the storage yard to handle the gigantic quantities of reinforcing steel that accumulate prior to loading. This machine is very compact and simply delivers good lifting performance.
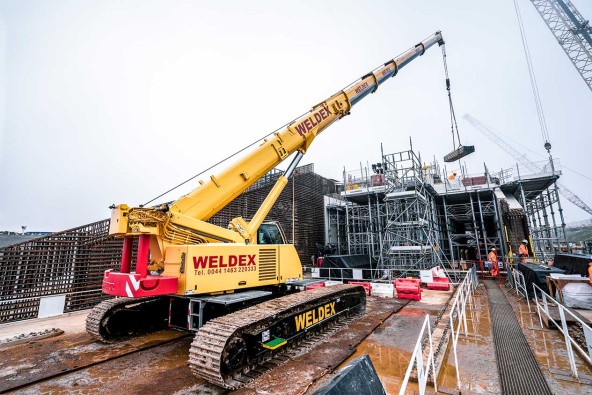
Why are LTR cranes so popular on these large construction sites?
Mark Hollett: The popularity of this type of crane has grown immensely in recent years. It has been well received in the market, partly because our end customers have now become familiar with the advantages of these units. For this kind of tunnel construction, speed and versatility thanks to the telescopic boom were clearly the decisive factors for the choice of these machines. And of course, they make it possible to transport material on the construction site. Generally speaking, I can say that our LTR cranes are among the busiest in our fleet. The ability of these cranes to roll off the low-loader at the construction site, set themselves up without an auxiliary crane and simply be ready to work quickly is hugely advantageous. Especially in London, where there is often not enough space to mount a lattice boom.
Which LTR units can be found in the Weldex crane fleet?
Mark Hollett: We have them in all available load classes. The LTR 1040 was actually the result of our own initiative. Some of our customers wanted a smaller and lighter crane than the LTR 1060 and we asked Liebherr about it. Today, the 60 tonner is offered as the LTR 1040 without central ballast and without a ballasting device. The machine therefore has just 5.6 tonnes of ballast, but in many boom positions it actually offers significantly higher lifting capacities than a 40 tonne mobile crane. Our four LTR 1040s are really busy machines.
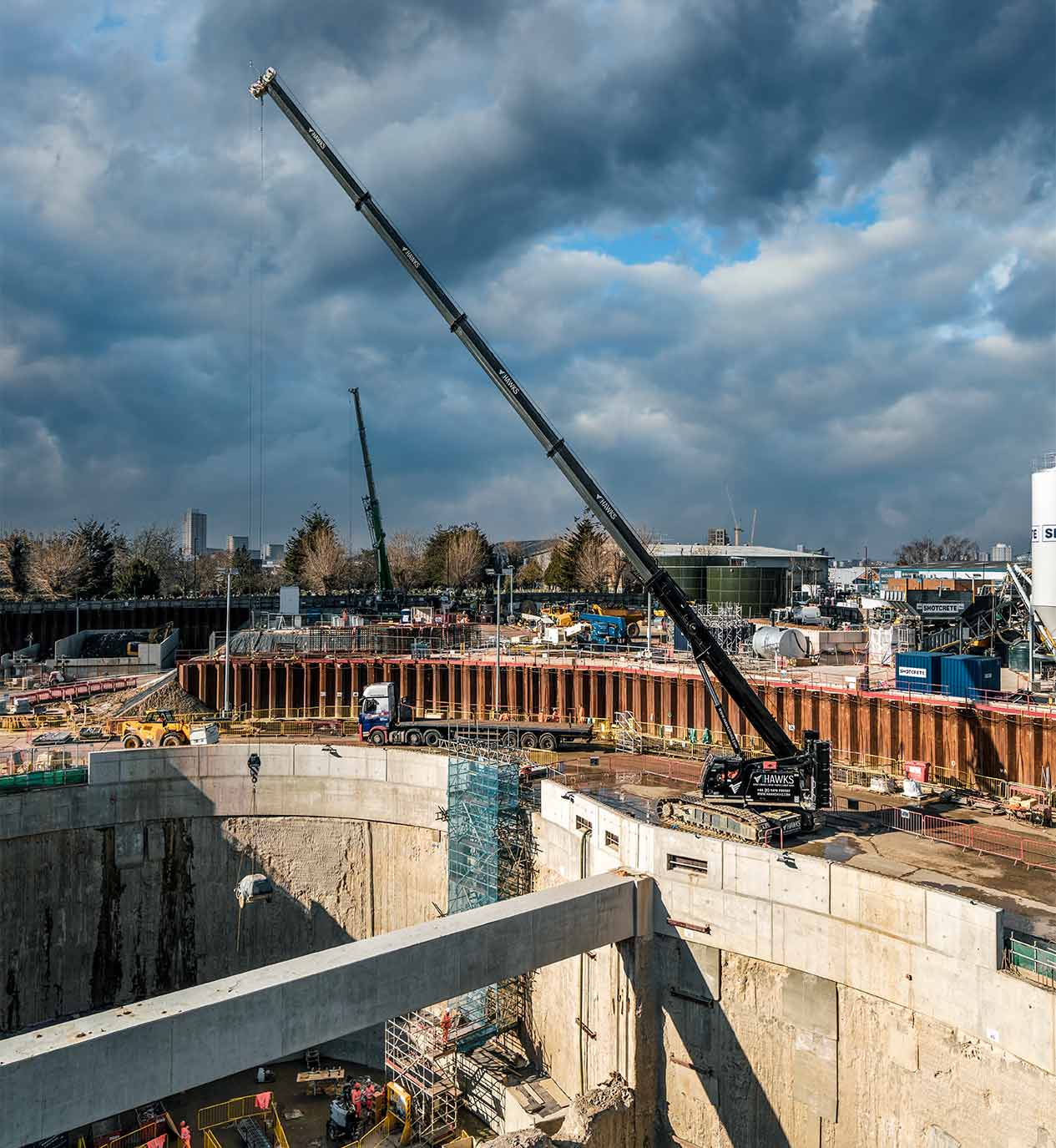
Elliot Hawkins, eight years ago you founded Hawks Crane Hire Ltd. You therefore have many years of practical experience with Liebherrʼs LTR machines. Whatʼs your verdict on our cranes?
Elliot Hawkins: Very good! We are delighted with your products. In addition to our eight large lattice boom crawler cranes, we operate seven Liebherr telescopic cranes with crawler travel gear. The LTR series is so practical simply because of the telescopic boom. The set-up times are extremely short and on huge construction sites like the ones we have here in London at the moment, the ability to move equipment or building materials quickly and efficiently is a huge advantage. The crane can move to another work location in only a short time. Compared to a mobile crane, which takes almost half an hour each time, we can save a lot of time. Here on the Victoria Road Crossover Box site, our LTR 1100ʼs mobility and speed as well as the telescopic 52 metre boom are indispensable.
The fact that Liebherr always has an open ear for us has really paid off. We can see from the upgrades or from the new machines, which often contain the improvements we requested previously, that the people at Liebherr not only listen to our suggestions, but also implement them where possible. I think this partnership is something special.
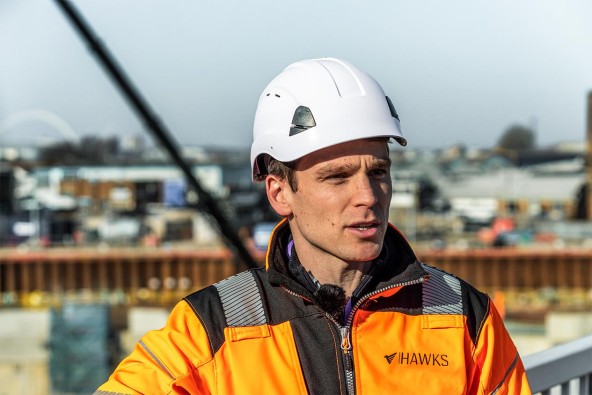
Elliot Hawkins - CEO and founder of Hawks Crane Hire Ltd.
Which lifting capacity classes does your fleet of tele-crawlers cover?
Elliot Hawkins: Our most powerful telescopic crawler cranes are the 100 tonne LTRs. But we want to increase both the number of cranes and their capacities. Specifically, we would like to have the LTR 1220 in our fleet in the future. In projects like “High Speed 2”, this performance class is often needed. And I have to say, we are impressed with the LTR units we use.
Mark Hollett: They are simply quality machines. With the LTRs, we rarely see a unit failure. And Weldex also appreciates the really good working relationship with Liebherr. The support from the manufacturer is fantastic. After all, if we didnʼt really like their machines, we wouldnʼt have bought 41 LTR crawler cranes from Ehingen.
This article was published in the UpLoad magazine 02 | 2023.