Focus on quality
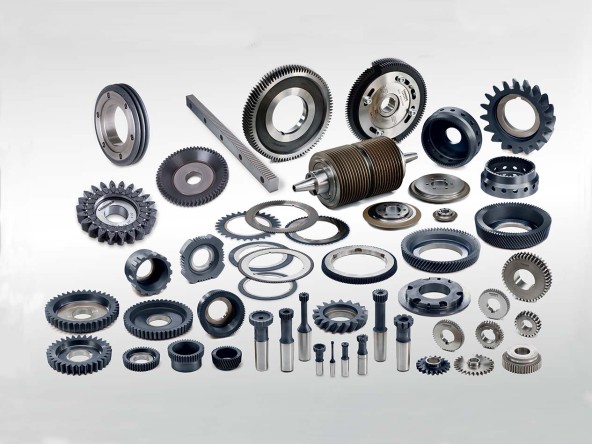
Gear cutting tool product range
Liebherr offers a comprehensive range of gear cutting tools, many years of experience in gear manufacturing, and the highest level of product quality down to the smallest detail. We are a reliable partner offering innovative developments and durable tools.
Our product range is in demand from customers all over the world. In addition to tool calculation, design and production, Liebherr offers all its customers excellent after-sales service. This includes sharpening and coating gear cutting tools as well as reconditioning CBN grinding tools at our electroplating shop.
Contents
Get an overview of our extensive portfolio on this page:
Stock tools
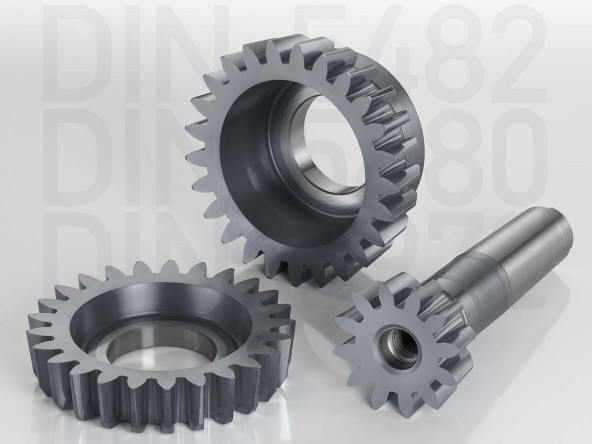
Find the right gear cutting tool with just a few clicks
Liebherr offers a wide range of high-quality shaper cutters.
We have disc, shank and bell cutters in stock.
Simply order them using the inquiry form in this catalog.
More information on our tools
Read exciting articles from our customer brochure