Bearing condition monitoring: Smart, digital and precise
The fast and precise measurements with the digital Liebherr smart slewing bearing and sensors enable you to maintain your applications and operations with maximum efficiency. This ensures an optimal bearing condition monitoring in numerous applications.
Beside of bearing clearance measurement Liebherr offers solution for bearing monitoring temperature and water content for various applications and areas. Find out more about the numerous applications for bearing condition monitoring!
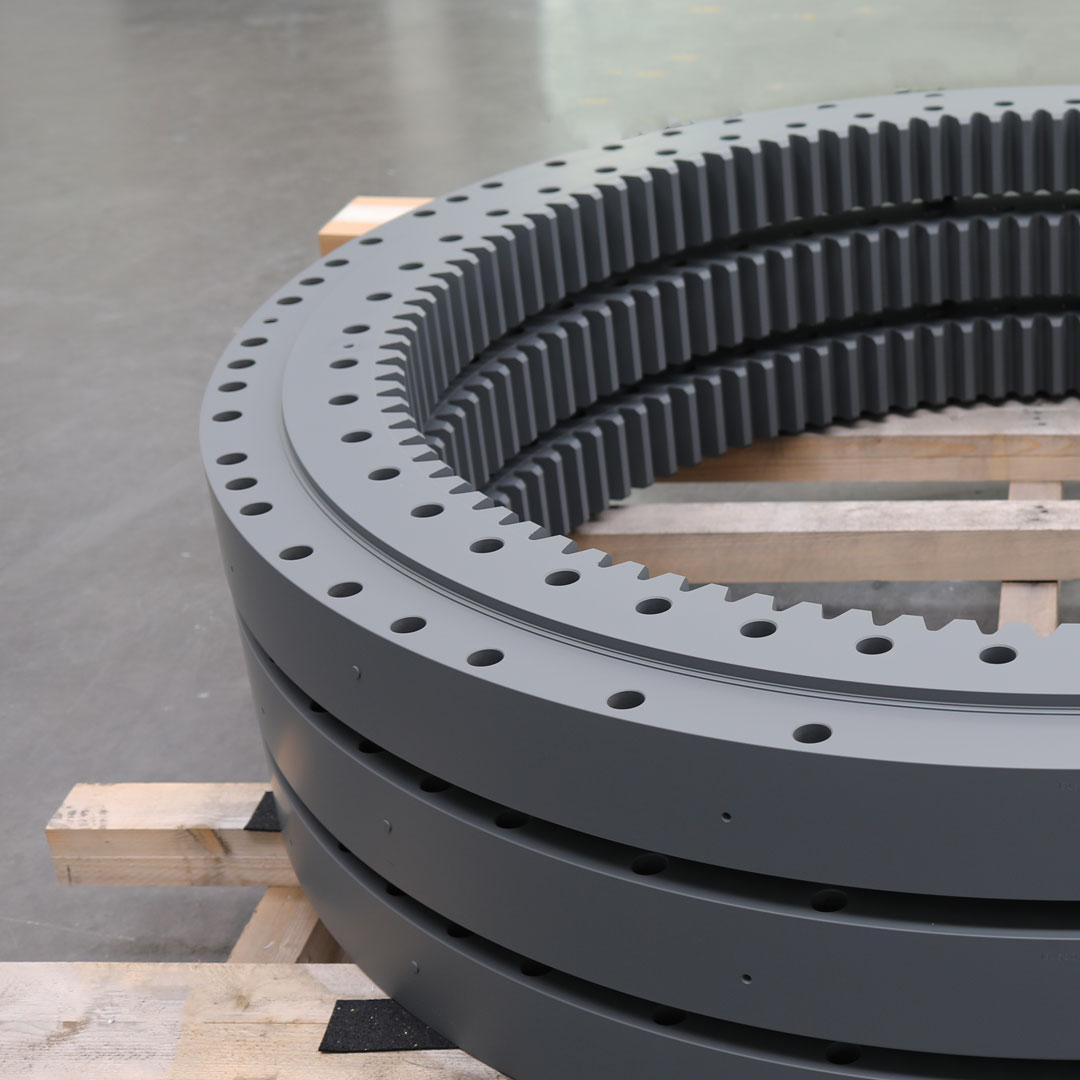
Reduced downtime: simple and fast
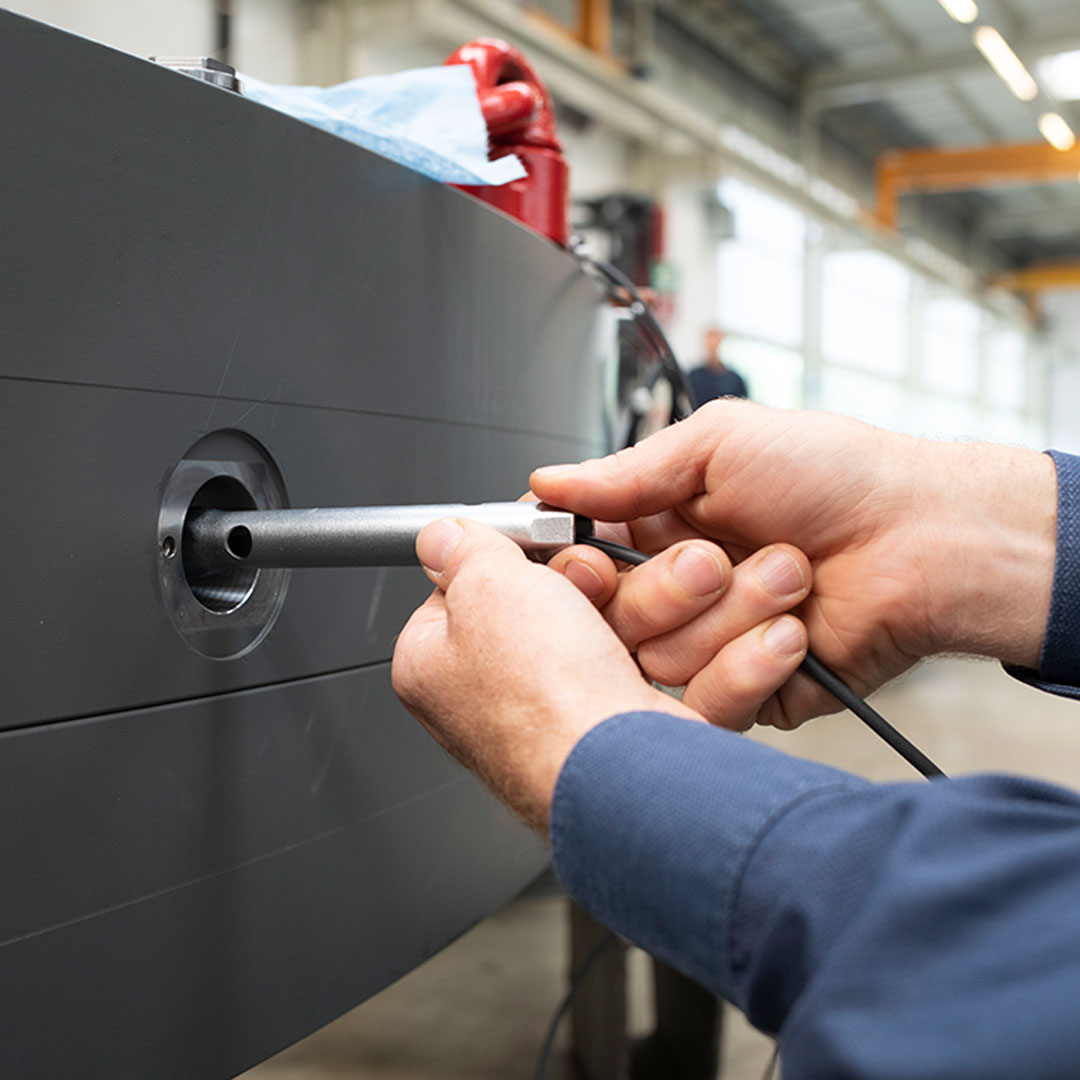
Safety: integrated and remote
.jpg)
Cost efficiency: save 75% or more
Application-specific solutions
Monitoring functions
Components Identification:Digitalized recognition of components and allocation of an end device.
Components Service: Condition monitoring (CM) involves querying the condition of the slewing bearing. This is classified in a trend analysis, which is used to create a forecast for the future. Based on CM, predictive maintenance can be introduced. With Predictive Maintenance information on the future condition of a component is predicted and recommendations for action are made based on this.
Component Update: Remote services also include flashing software that runs directly on a component.
Bearing clearance monitoring: This is how it works
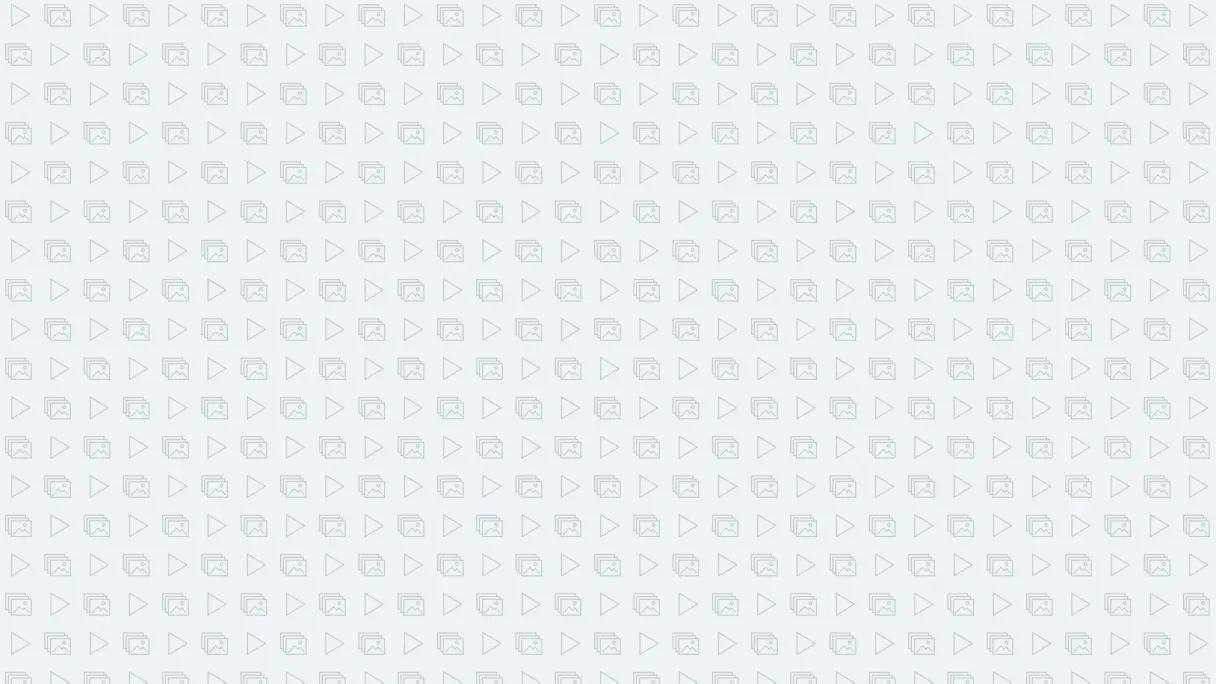
This video is provided by Google*. When you load this video, your data, including your IP address, is transmitted to Google, and may be stored and processed by Google, also for its own purposes, outside the EU or the EEA and thus in a third country, in particular in the USA**. We have no influence on further data processing by Google.
By clicking on “ACCEPT”, you consent to the data transmission to Google for this video pursuant to Art. 6 para. 1 point a GDPR. If you do not want to consent to each YouTube video individually in the future and want to be able to load them without this blocker, you can also select “Always accept YouTube videos” and thus also consent to the respectively associated data transmissions to Google for all other YouTube videos that you will access on our website in the future.
You can withdraw given consents at any time with effect for the future and thus prevent the further transmission of your data by deselecting the respective service under “Miscellaneous services (optional)” in the settings (later also accessible via the “Data protection settings” in the footer of our website).
For further information, please refer to our Data Protection Declaration and the Google Privacy Policy.*Google Ireland Limited, Gordon House, Barrow Street, Dublin 4, Ireland; parent company: Google LLC, 1600 Amphitheatre Parkway, Mountain View, CA 94043, USA** Note: The data transfer to the USA associated with the data transmission to Google takes place on the basis of the European Commission’s adequacy decision of 10 July 2023 (EU-U.S. Data Privacy Framework).