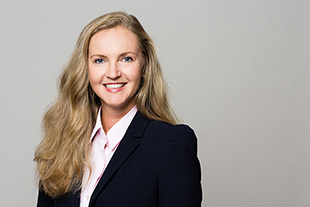
Alexandra Nolde
Senior Communication & Media Specialist
Liebherr-Components AG
Brown Boveri Strasse 7
5400 Baden
Switzerland
- Phone+41 562 9643-26
- Fax+41 562 9643-01
A diagnostics staff member in the Components Division of Liebherr in Ettlingen (Germany) has made a splash with the Smart Klaus: The optical detection solution correctly identifies individual parts within seconds, thereby significantly increasing efficiency.
At Liebherr-Ettlingen GmbH, the Reman competence centre of the Liebherr Group, precise individual identification of used parts is an important building block of business activity. The factory specializes in the remanufacturing of used drive components such as engines, gearboxes and hydraulic components. They are overhauled, repaired or assembled with exchange components or assemblies from parts in stock.
Every day, apart from other components, up to seven worn-out diesel engines of excavators, wheel loaders, mobile cranes or other construction vehicles are delivered to the yard in Ettlingen. Mechanics dismantle them and the recyclable items are washed, stripped, de-rusted, then diagnosed, provided with the correct identification number and finally stored systematically in a high-bay warehouse.
By now, the parts of the returned and dismantled components have to be identified using drawings and manual measurements, and this has been very time-consuming. “This means up to 100 parts or more per engine, which need to be identified” explains Andreas Just. With over 600 engine variants in the portfolio, the number of different individual parts is enormous. Although the mechanics recognise some of them at a glance, in many cases however, they have to examine the design drawings very closely and to compare each detail. “It sometimes takes four to five minutes,” explained Just, “especially for pipes with different bends and lengths or for complex parts with different bores.” This requires looking very carefully and measuring to avoid any confusion, because otherwise the part does not fit when assembling an exchange engine. This is exhausting, excruciating work because any part incorrectly stored with the wrong identification number can lead to delays in assembly and endanger rapid processing times.
This had long been a source of frustration for Andreas Just. He, therefore, looked specifically for an optical detection solution. And he found one in the Smart Klaus of the company Optimum datamanagement solutions GmbH from Karlsruhe (Germany). He immediately saw that the Smart Klaus drastically reduces throughput times - by more than 50 percent -, increases productivity, provides security in identification and frees up time for highly skilled work.
At Liebherr-Ettlingen GmbH, the Reman competence centre of the Liebherr Group, precise individual identification of used parts is an important building block of business activity. The factory specializes in the remanufacturing of used drive components such as engines, gearboxes and hydraulic components. They are overhauled, repaired or assembled with exchange components or assemblies from parts in stock.
Every day, apart from other components, up to seven worn-out diesel engines of excavators, wheel loaders, mobile cranes or other construction vehicles are delivered to the yard in Ettlingen. Mechanics dismantle them and the recyclable items are washed, stripped, de-rusted, then diagnosed, provided with the correct identification number and finally stored systematically in a high-bay warehouse.
By now, the parts of the returned and dismantled components have to be identified using drawings and manual measurements, and this has been very time-consuming. “This means up to 100 parts or more per engine, which need to be identified” explains Andreas Just. With over 600 engine variants in the portfolio, the number of different individual parts is enormous. Although the mechanics recognise some of them at a glance, in many cases however, they have to examine the design drawings very closely and to compare each detail. “It sometimes takes four to five minutes,” explained Just, “especially for pipes with different bends and lengths or for complex parts with different bores.” This requires looking very carefully and measuring to avoid any confusion, because otherwise the part does not fit when assembling an exchange engine. This is exhausting, excruciating work because any part incorrectly stored with the wrong identification number can lead to delays in assembly and endanger rapid processing times.
This had long been a source of frustration for Andreas Just. He, therefore, looked specifically for an optical detection solution. And he found one in the Smart Klaus of the company Optimum datamanagement solutions GmbH from Karlsruhe (Germany). He immediately saw that the Smart Klaus drastically reduces throughput times - by more than 50 percent -, increases productivity, provides security in identification and frees up time for highly skilled work.
Only a few parameters are sufficient for optical identification
Since January 2018, the Smart Klaus has been integrated into the working process in Ettlingen. The "intelligent colleague" has been gradually trained by highly qualified professionals. By early February, more than 1,500 parts have been entered, and this number had already reached more than 5,000 in the summer. "Weight and contour are the main features that we teach the Smart Klaus. If this is not enough to recognise a part with more than 90% certainty, we can additionally enter up to 100 special features - from the number and diameter of bores through gear wheels to reflections, typography or surface texture,” explains Andreas Just. Although each additional feature slows down the identification, which is why as few parameters as possible are entered, the Smart Klaus is still incredibly fast with many parameters. A 90 percent security of identification is enough to attribute the correct identification number. “It usually recognises a part in 10 to 20 seconds,” says the team leader of the diesel department in Ettlingen, Sebastian Kurpiers. The speed of the Smart Klaus increases productivity at the same time. Because the significantly faster processing time increases the number of parts in stock and, thus, offers capacity to accelerate the assembly of exchange engines and to handle more Reman jobs.
However, it is not the faster processing time that matters, but the time it saves for qualified specialists. They can now use their high level of expertise to further increase quality standards, measure parts in a more targeted manner and eliminate sources of error.
Wide range of possible applications
The Smart Klaus accelerates the working process immensely and creates capacity for future challenges. The variety of parts will increase significantly in the coming years. Between 2,000 and 2,500 new parts are added with every new generation of engines, and they will have to be captured by the software. It will no longer be possible to identify and document them without the technical support provided by the Smart Klaus and the staff. Ettlingen is, therefore, thinking about using the recognition system in other departments. After this initial experience, there is a high degree of confidence in the technology of the Smart Klaus and in its possibilities for other future applications.
> Learn more about the Reman-Program: www.liebherr.com/reman
Here you will find the press release and images for download.
Senior Communication & Media Specialist
Liebherr-Components AG
Brown Boveri Strasse 7
5400 Baden
Switzerland