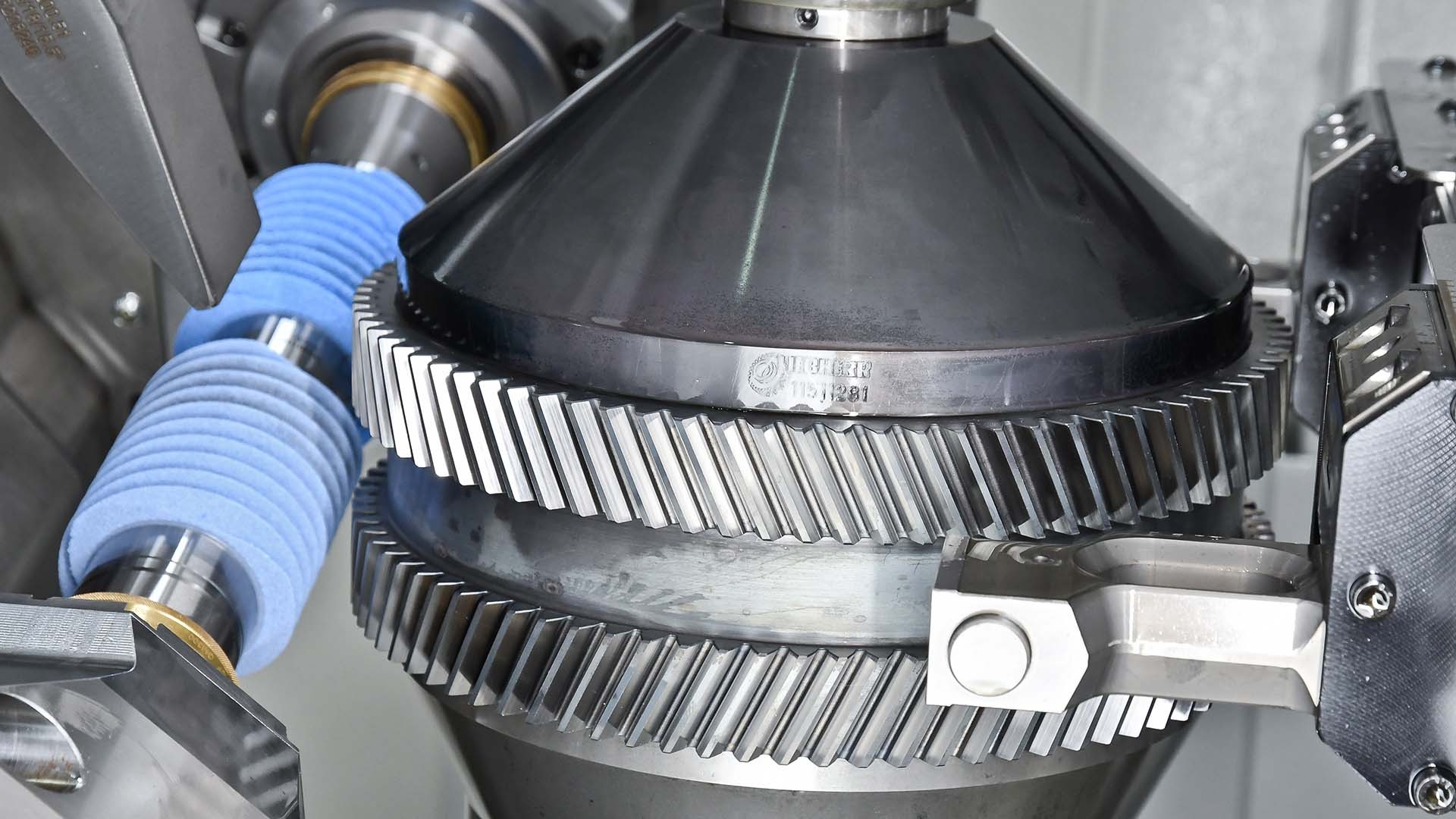
Generating grinding of double helical gears
In future, generating grinding can also be used under certain conditions to produce double helical gears. This means Liebherr-Verzahntechnik GmbH is expanding its range of processes for hard-finishing for this gear type to meet the highest quality requirements. Compared to established processes such as profile grinding or hard milling, generating grinding is much faster and therefore also provides an interesting alternative from a commercial perspective.
Double helical gears combine the advantages of both spur gears and helical gears: transfering of high forces, quiet running behavior due to increasing the contact ratio, and a reduced axial bearing load. They are used wherever a high power density is required from the gears. Their range of applications extends from very small, lightweight and compact parts in aerospace to powerful turbo transmissions and very large-scale applications in energy and materials handling technology.
Generating grinding – an efficient alternative in hard-finishing
Today, due to increased quality requirements in terms of their efficiency, quiet running and noise development, double helical gears increasingly need to be hard-finished. For manufacturing reasons, only 4 or 5-axis hard milling is possible for continuous double helical teeth with no gap between the top and bottom gears. Profile grinding has become established in most cases for double helical gears. Liebherr-Verzahntechnik GmbH has now succeeded in developing generating grinding as a precise and efficient alternative for this hard-finishing. With Liebherr having already optimized the soft machining of double helical gears by means of precise correction measurement in gear shaping, the company is now taking hard-finishing to a new level: The cycle times can be up to ten times faster when compared to profile grinding. The quality produced meets the very highest accuracy and surface roughness requirements. The workpiece simply has to meet the following requirements: the distance between the two gears is at least 23 millimeters and the module must not be larger than 5.
Advantages of generating grinding
− Significantly shorter grinding times
− More resistant to stock variation and hardening distortions
− Lower risk of grinding burn
− Efficient manufacture of topological modifications
− Improved accuracy in the apex point and in the angular position of gear teeth
− Excellent individual pitch accuracy, and cumulative pitch overall quality
− Potential for finish grinding and polishing to improve surface quality
− Combination with fully automatic stock and material removal check possible
High-performance cutting materials
This has been made possible, for example, due to the development of robust grinding materials enabling the economic application of worms with a very small diameter. Triangular or rodshaped sintered corundum grinding material or CBN (cubic crystalline boron nitride) with a galvanic or ceramic bond are used as cutting materials. Liebherr is able to offer the optimal cutting material according to the application and requirements.
Two grinding worms on one arbor
To ensure minimal tool overtravel, two grinding worms are used whose lead direction matches the gears to be ground in each case: the left-handed gear on the double-helical is machined with a left-handed grinding worm, the right-handed gear is machined with a right-handed grinding worm. The two grinding worms are on a long arbor and are controlled by software with the gear being machined consecutively, in one clamping. Each of the two worms can both rough and finish the workpiece. The worms are designed in the CAD model with the aim of maximizing their outside diameter and their length. “We approached the design of the worms with the view that ultimately we were just adding another gear with another helix angle – as simple as that. We tried that out, and the trials were successful,” says Dr. Andreas Mehr, an expert in gear grinding at Liebherr, recounting the development with a slight twinkle in his eye.
Highest quality in gear geometry
In the generating grinding process itself, the grinding of the upper gear is completed first. This serves as a reference for the angular position of the two gears in relation to one another. Via an adapted centering process, the lower gear is then very precisely ground with position orientation in relation to the first gear. Machining both in one clamping fixture enables an outstanding pitch to be achieved. This means that the distance, for example, from one left tooth flank to the next is virtually perfect. The axial position of the gear wheels in relation to one another – the apex point – is achieved using this technology with a very high degree of precision. Besides the significantly faster machining times, generating grinding has other advantages compared to profile grinding: the method is more resistant to stock variation and distortion due to heat treatment.
In addition to the precise apex point, it also achieves much greater precision in the angular position (index) of the two gears in relation to one another. It also improves the surface roughness and provides greater stability when grinding the dedendum contour. The individual quality of the lead and the lead quality overall is very high thanks to the continuous process. This means that topological modifications such as specific end reliefs or twist-free grinding can be manufactured economically. The risk of grinding burn is also lower.
Rough application guideline and limits
Criteria | 4-axis-milling | Profile grinding | Generating grinding |
Module | 1 – 50 mm | 1 – 30 mm | 1 – 5 mm |
Production | Single part | Single to medium | Medium to mass |
Green machining | Yes | Limited | Limited |
Hard machining | Yes | Yes | Yes |
Gap size | 0 mm | 15 mm | 25 mm |
Gear quality | ISO 5 | ISO 3 | ISO 5 |
Index accuracy | +/- 15 µm | +/- 30 µm | +/- 20 µm |
Surface finish | Rz 2-10 µm | Rz 2-4 µm | Rz 3-6 µm |
Grinding head and software requirements
For the generating grinding of double helical gears, a powerful and dynamic grinding head with a counter bearing is required which enables machining with both small and long grinding worms. Liebherr’s newly designed GH 240 CB grinding head is suitable for this. It has both main and counter bearings to rigidly clamp the tools, and achieves a maximum spindle speed of 12,000, or even the option of 17,000 revolutions per minute. Just as important is software with simple entry and correction options which are easy to understand, which is designed for double helical gears and which enables individual gears and their angular position to be corrected in relation to one another. With the relevant programming, the re-grinding function even enables the first part to be manufactured as a good part.
Retrofittable in existing machines
The process can be retrofitted on existing Liebherr LGG gear grinding machines provided they are fitted with the GH 240 CB grinding head and the LHGearTec control system. Its design, shift length and the option for also clamping small grinding worms mean the grinding head is the essential basis for the generating grinding of double helical gears. Liebherr examines every use case individually and helps to achieve the highest quality using its expertise and its process know-how. “We can develop a tailored solution for every customer,” explains Dr. Mehr.