Press releases | 14/09/2021
Liebherr Mining introduces data-driven Digital Services
- Liebherr Mining’s new Technology Product portfolio has been launched at MINExpo 2021, including the Digital Services suite.
- The new services use machine-generated data to provide rich data and insights required to drive fleet performance, increase utilisation, enhance machine health and availability, and improve the customer’s service journey.
- Building on the foundation of technical information in the Content Delivery Portal and troubleshooting function of the Troubleshoot Advisor, the new Remote Support Solutions will offer real-time 24/7 digital support from Liebherr experts.
To further support their customers with equipment performance and maintenance, Liebherr Mining has developed a suite of data-driven Digital Services as part of their new Mining Technology Product portfolio.
Las Vegas (USA), 14 September 2021 – Liebherr has presented the world premiere of its new Mining Technology Product portfolio at MINExpo 2021, which defines the company’s interoperable and scalable approach to its equipment, technology, and service product offerings. The Liebherr Mining Technology Product portfolio includes Digital Services, Assistance Systems & On-board Analytics, and Machine Automation product lines, providing customers with flexible scope of supply solutions to increase safety and asset operational effectiveness.
Together, these products will support operator’s performance, optimise diagnostic processes, and automate machine functions, whilst integrating machine data and OEM expertise within the customer’s chosen technology landscapes.
Alongside on-board technology solutions, Liebherr has unveiled its portfolio of new Digital Services. Digital services are connectivity enabled services that utilise data generated on the machine to provide customers with rich data and insights required to drive fleet performance, increase utilisation, enhance machine health and availability, and improve the customer’s service journey. Digital Services also enable remote monitoring of mining operations, reducing the time and costs related to manual data gathering, and allow mine management to focus on maximising overall mine performance. Beyond that, Digital Services enable the integration of Liebherr’s technology, engineering knowledge, and mining expertise with customer’s technology landscapes in order to maximise value generated from machine data. The portfolio includes three products: MyAssets, MyOperations, and MyMaintenance.
Increase availability with MyAssets
MyAssets is a service for maintenance and machine support roles who work to ensure maximum machine availability. It provides detailed and real-time insights on machine health conditions via the MyAssets application, allowing users to detect technical issues at an early stage thus minimising the risk of machine downtime. Some of the key functions within MyAssets include:
- Machine health overview: intuitive and real-time information about machine and fleet health conditions. Possibility to access historic information to carry out more detailed analysis.
- Machine events: access to detailed fault code information and historic records to investigate root cause and derive the most appropriate action plan.
- Operational conformance: insights related to compliance with operational and safety guidelines. It helps mine management to identify activities that could cause damage to the machine or compromise the safety of people on the mine.
Maximise productivity with MyOperations
MyOperations is a service for management and production roles who require constant monitoring of load and haul operations and work to maximise productivity and equipment utilisation. MyOperations identifies inefficiencies in the load and haul process and supports investigation of root causes so they can be eliminated to restore full productivity. The service also provides rich data and insights on machine and fleet performance, all through an intuitive application compatible with mobile devices. Some of the key functions within MyOperations include:
- Machine Operations overview: detailed insights and high-level overview of main production KPIs, to understand progress towards achieving production targets. Analyses status quo and evolution against past trends to gain insights on the dynamics of mine productivity.
- Optimisation potentials: function that automatically detects potentially inefficient operations, notifies the user, and supports the investigation of root causes.
- Application severity analysis: multiple indicators and an overall Application Severity score to provide users with an accurate assessment of the severity of machine application. Additionally, application severity events are geolocated, therefore areas in the mine with higher Application Severity are easily identifiable and measures to reduce damage to machines can be adopted early on.
Expert troubleshooting with MyMaintenance
MyMaintenance is a suite of applications designed to support maintenance teams and accelerate the execution of jobs from investigation, to preparation and resolution, including documentation. MyMaintenance includes a combination of solutions that provide access to accurate and up-to-date technical documentation for service technicians and planners, improved communication between field and support staff, and remote support tools to liaise with Liebherr experts:
- Liebherr Troubleshoot Advisor (TSA) is an intuitive platform providing access to detailed troubleshooting instructions for common technical problems, enabling customer’s onsite technicians to troubleshoot their equipment as a Liebherr expert would. Available both online and offline, users can follow a step-by-step process to connect to the app, select the problem, and search for solutions.
- Liebherr Content Delivery Portal (CDP) is a user-centric, intelligent search database comprising all Liebherr Mining technical documentation from operating manuals to assembly instructions, allowing users to locate relevant information quickly and precisely. The CDP has several useful functions including an offline mode, smart search, personal collections, bookmarks, document alerts, and more.
- Liebherr Remote Support Solution is a new service that builds on the foundation of technical information in the CDP and troubleshooting function of the TSA to offer real-time 24/7 digital support from Liebherr experts. With multiple subscription options providing the level of support suited to each customer, the Remote Support Solution leverages Liebherr’s technical expertise and global support network to bring equipment back to operation as quickly as possible.
Downloads
Here you can find the press release and images for download.
Contacts
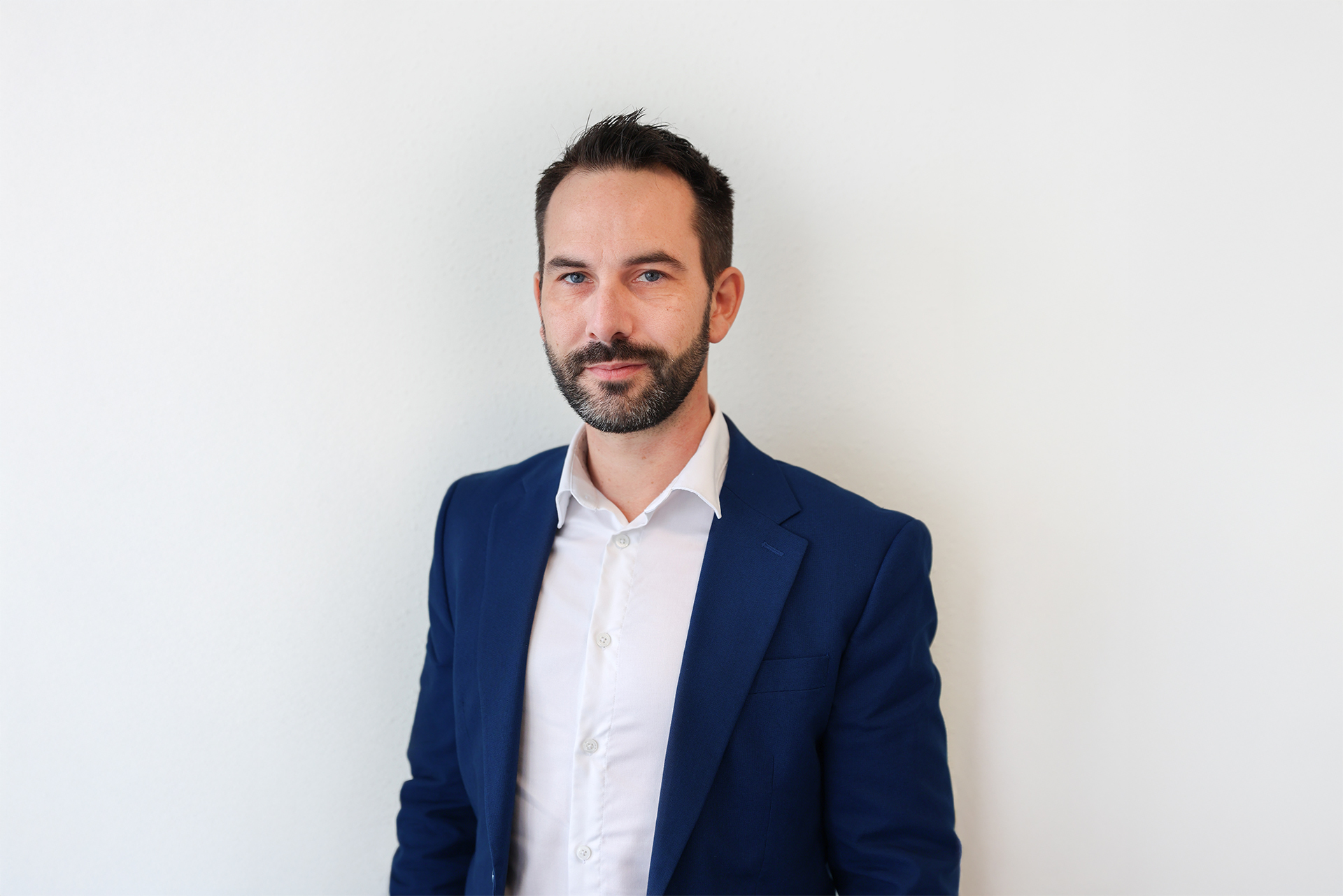
Liebherr Mining Equipment Newport News Co.
Newport News, VA 23607
United States of America