Open-technology approach
The reduction of global greenhouse gases is a significant challenge of our generation. Striving to reach net zero emissions in the future, Liebherr works on alternative and climate-friendly powertrain concepts.
Thereby, the Liebherr team pursues an open-technology approach. In the field of internal combustion, the focus of the research and development activities lies on multiple solutions, depending on the needs different fields of application will require in the future. Being a promising, carbon-free energy source, hydrogen is one of the options to power an internal combustion engine that builds a bridge to other alternate fuels.
Liebherr is convinced
that ICE will remain an important solution for heavy-duty and off-highway vehicles
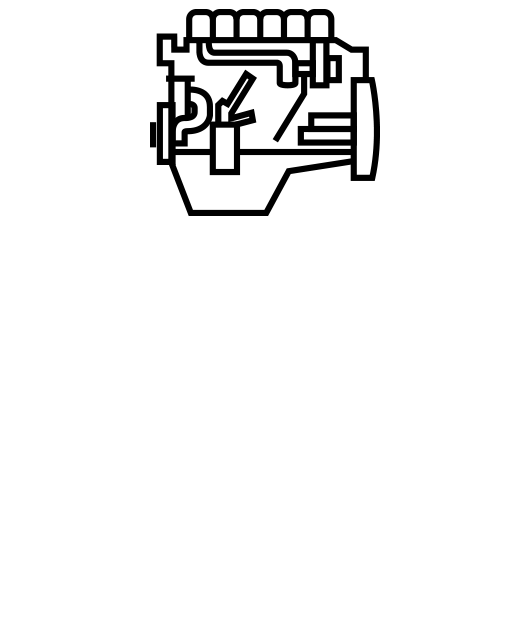
PFI injects at pressures up to 15 bar into the air intake system. The uniform mixture homogenization in the intake manifold results in lower NOx emissions. Moreover, port fuel injectors work in less demanding operating conditions and as a consequence, time to market is much faster.
DI injects at pressures around 30 bar directly in the combustion chamber using a low-pressure process. The power density is similar to that of a diesel engine. DI is particularly well suited for applications with high demands on dynamics and power density within a limited installation space, such as mobile construction machinery.
Want to know more?
Contact our sales team or follow us on our LinkedIn channel